Ballymena -based soft drinks manufacturer, Norbev has increased its turnover by over 50 per cent following an investment of almost £300,000 in the up-skilling of its staff. Founded in 1919,
Supply chain
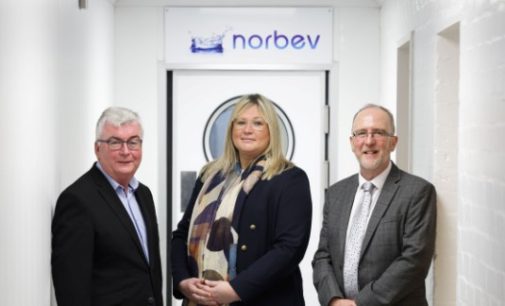
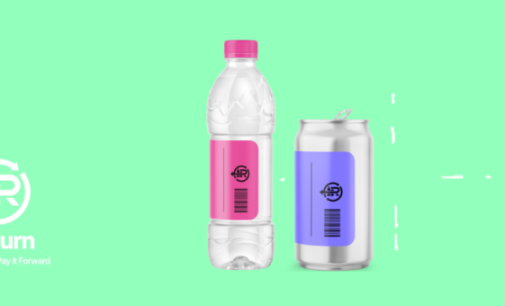
Ireland’s Deposit Return Scheme, Re-turn, has achieved a significant milestone, collecting over 20 million drinks containers since its inception on February 1. This achievement was reached on March 29. Re-turn recorded
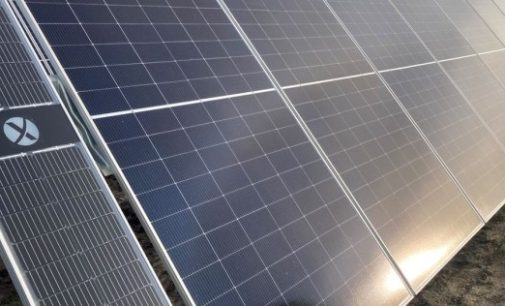
75% of the electricity now being used to make Britvic soft drinks in Great Britain – from Fruit Shoot to Tango, Robinsons to J2O – is coming from a 160-acre
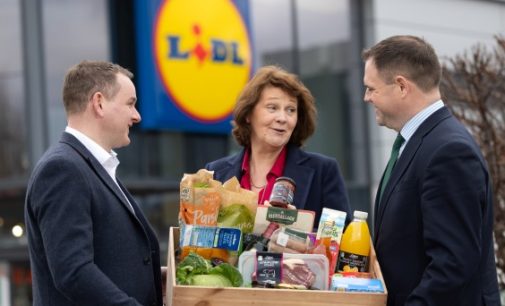
Lidl Ireland has announced that more than €1.6 billion worth of goods and services was procured from Irish suppliers and business partners by the retailer in 2023. A total of
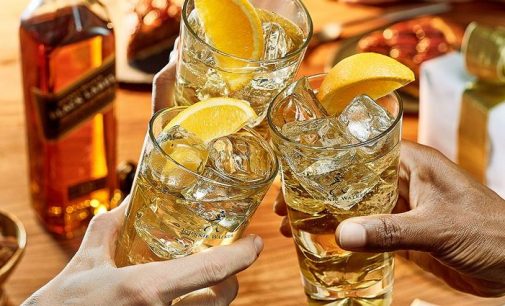
A new report from Oxford Economics shows that Diageo – a global leader in beverage alcohol, with brands including Johnnie Walker, Smirnoff, Baileys and Guinness – is contributing over €13
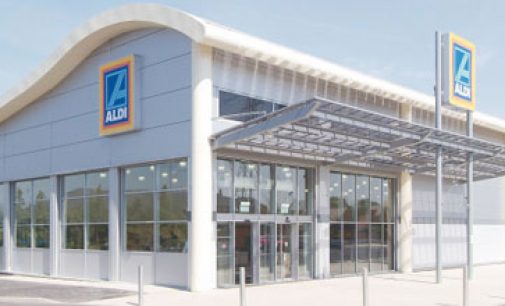
ALDI has announced that it has spent €1.1 billion with Irish suppliers in 2023, a year which saw the opening of six new stores and ALDI being voted the most
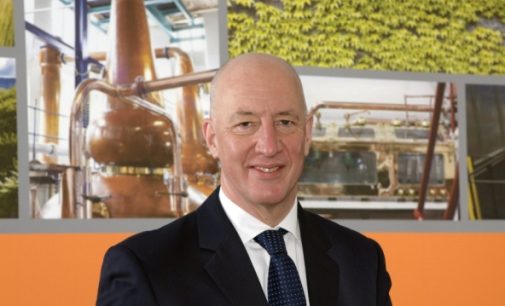
The contribution of the Scotch Whisky industry to the UK economy reached £7.1 billion in 2022. A new report by the Scotch Whisky Association (SWA) also reveals the industry supports
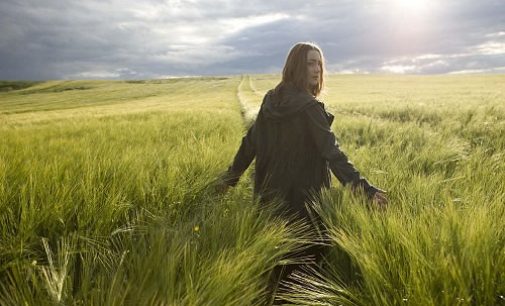
Bord Bia has acknowledged the sustainability performance of 97 Irish food and drink companies that have attained Origin Green Gold Membership in 2023. Gold Membership is given to companies, which
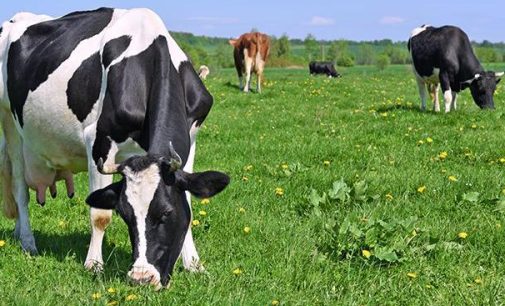
Dairy Industry Ireland (DII), the Ibec association representing the sector, has unveiled a new comprehensive report that highlights the substantial economic contribution, global market potential, and commitment to sustainable practices
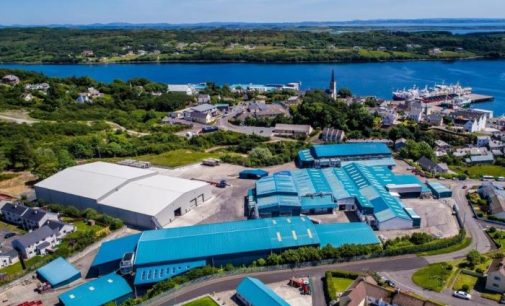
Killybegs in County Donegal, which one of Ireland’s busiest seafood hubs, is to benefit from a total €50 million investment aimed at future-proofing the region’s fish processing sector and maintaining
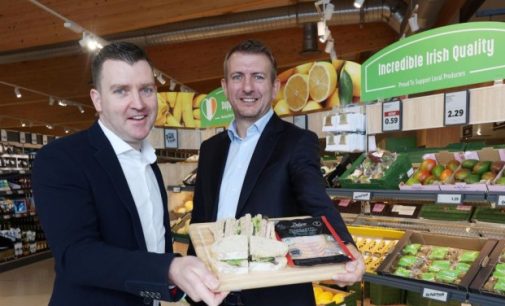
Lidl Ireland has announced a major supply deal with Kildare-based cooked meats producer, O’Brien Fine Foods, valued at €60 million. This new deal will see O’Brien Fine Foods supply to
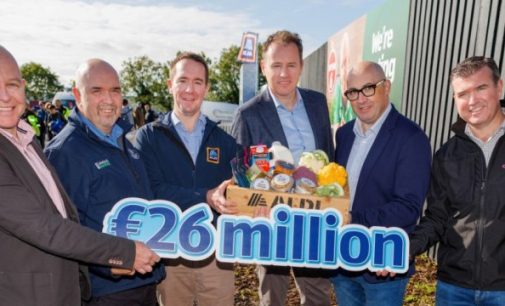
ALDI Ireland has agreed four major new deals with Irish-based suppliers worth more than €26 million. The new and extended contracts continue ALDI’s long-standing commitment to its Irish supplier network,
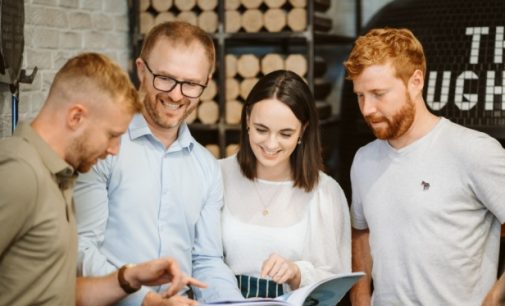
Ifac, Ireland’s farming, food, and agribusiness specialist professional services firm and a top 10 accountancy firm, has published its sixth annual Food and Agribusiness Report 2023 – the only report
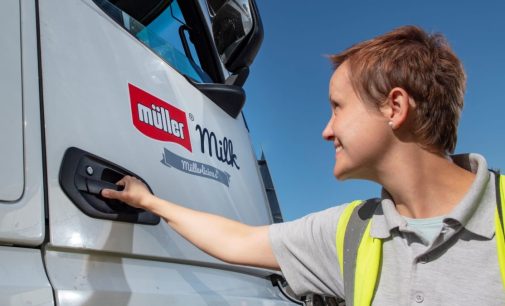
Müller Milk & Ingredients, which produces branded and private label fresh milk, cream, butter, milk drinks and ingredients products and boasts a network of dairies and depots servicing customers throughout
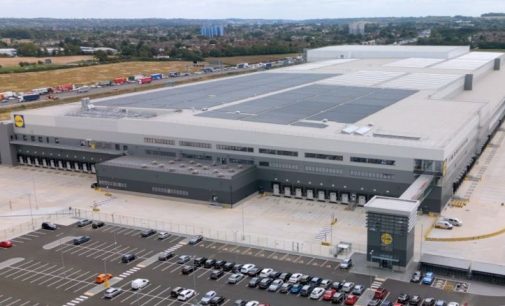
Lidl GB has officially opened its £300 million RDC – the largest Lidl warehouse in the world – marking the discounter’s continued commitment to expansion across Great Britain. The 1.2
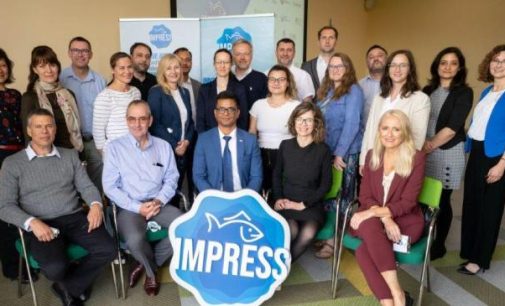
IMPRESS is an industry driven project, based on sound science and centred around the EU Bioeconomy and Blue Growth strategies, striving to promote sustainable and zero-waste production and consumption. The

The Scotch Whisky Association (SWA) has published a Water Stewardship Framework, offering research-based guidance for the Scotch Whisky industry as it works to improve efficiency and make reductions in its
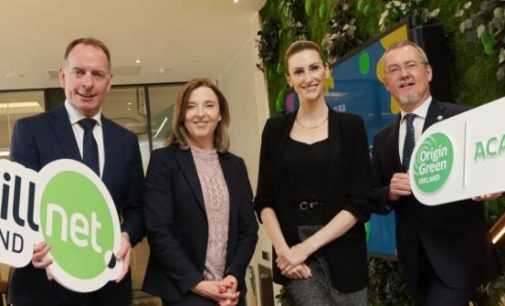
Bord Bia and Skillnet Ireland have launched the Origin Green Academy to develop sustainability skills and talent for the Irish food and drink industry. Bord Bia has partnered with the
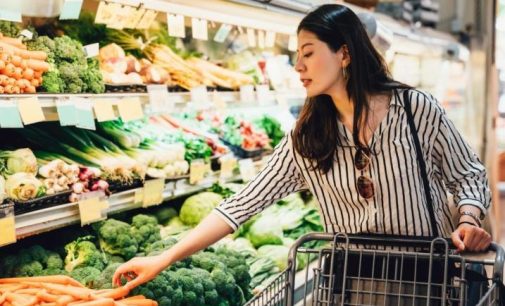
The National Standards Authority of Ireland (NSAI) has announced that it has now certified more than fifty companies in Ireland to an international certification scheme for food safety management systems.
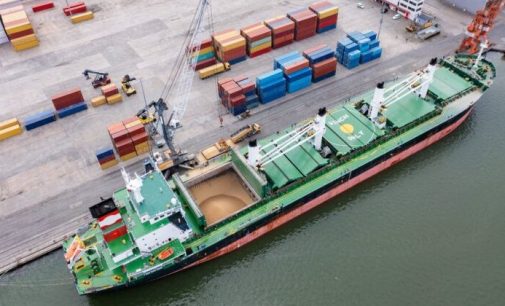
UK Research and Innovation (UKRI) has added a new £680,000 interdisciplinary project to its Transforming UK Food Systems Strategic Priorities Fund (SPF) programme. The successful project, led by the University of
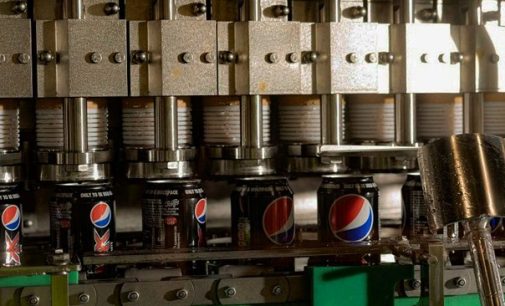
Leading soft drinks business, Britvic, is announcing a further £13 million investment into a fifth canning line at its Rugby factory in England. Based on the Glebe Farm Industrial Estate,
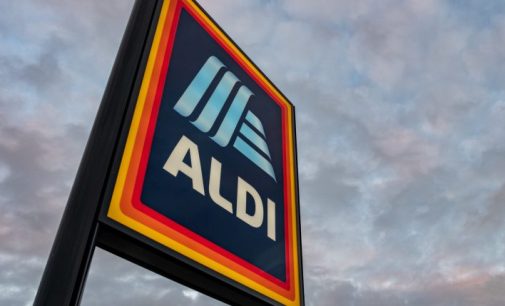
In 2022, ALDI sourced €1.1 billion of locally produced food and drink from Irish suppliers. In total, ALDI partnered with over 330 Irish producers throughout the year, including long-term relationships with Twomey’s
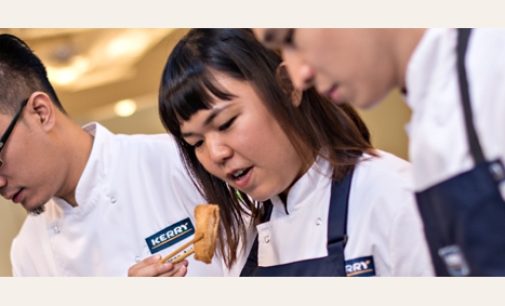
Kerry Group, a world leader in taste and nutrition for the food, beverage and pharmaceutical markets, has announced details on
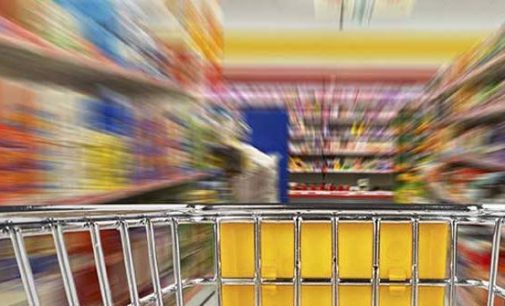
Global insight provider IGD has identified six trends set to influence the global retail landscape in 2023. With inflation driving
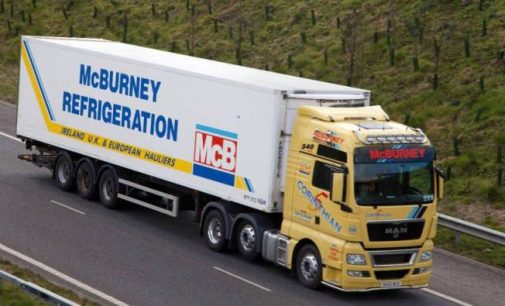
DFDS, the European ferry and transport services giant, has agreed to acquire 100% of McBurney Transport Group headquartered in Northern
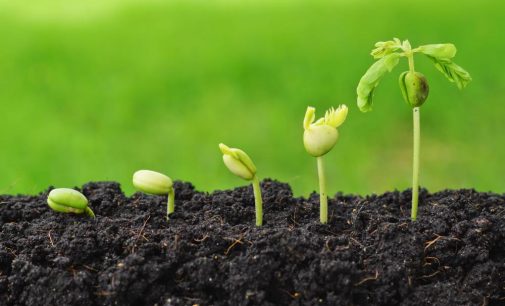
A new report, by economists at Teagasc, provides the latest estimates of average incomes for various farm types in 2022
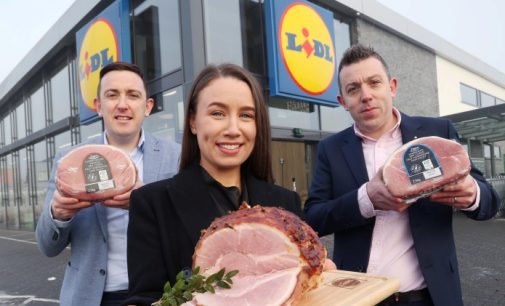
Lidl Ireland has announced a new contract worth more than €17 million with Honeyvale Foods. The new deal will see
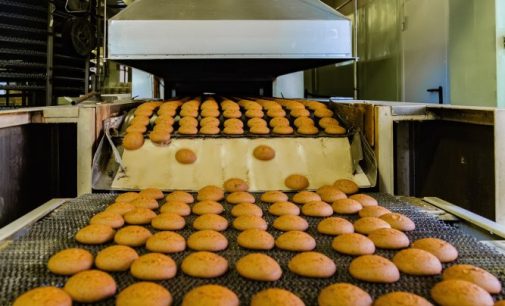
Nearly 50% of food and drink manufacturers have cut or paused investment projects as they face the toughest trading conditions
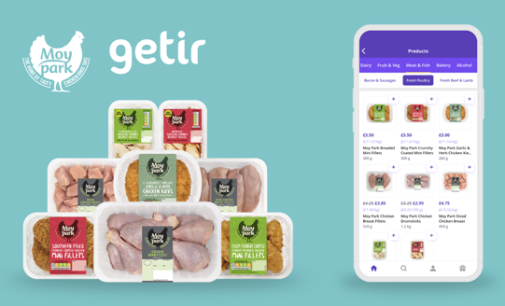
Leading UK food company, Moy Park, has secured a supply deal with, Getir, which will see eight of its Moy
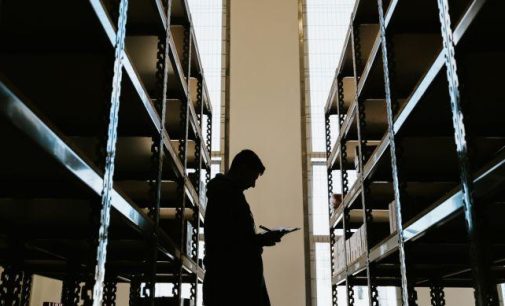
Stock inefficiencies and inventory ‘black holes’ are exacerbating the supply chain crisis for food companies according to new research. Nearly 10% of

Mondelēz International, makers and bakers of iconic brands including Cadbury, OREO and Maynards Bassetts, has launched its latest economic and
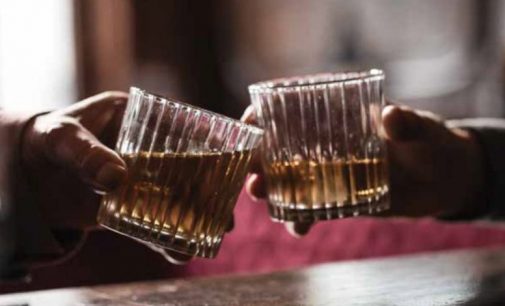
92% of Irish whiskey producers have said that supply chain delays have negatively impacted on their recent production output and
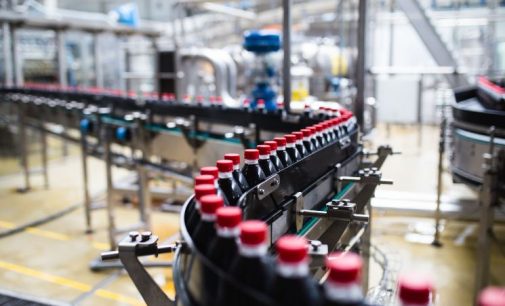
Leeds-based CO2Sustain is reminding carbonated drinks manufacturers that its patented additive can cut by 12% the amount of CO2 needed to add fizz during
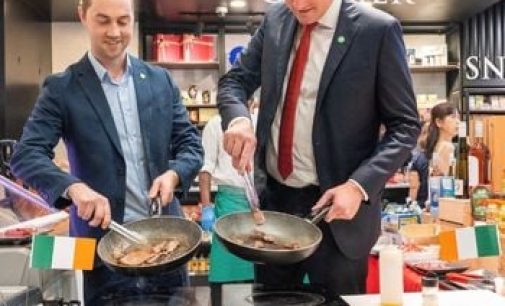
Consumers in Singapore can purchase Irish beef and lamb in store for the first time at retailer, Ryan’s Grocery. Seven
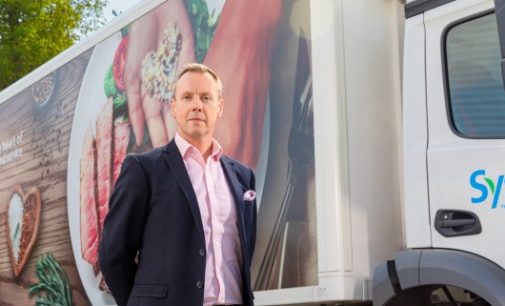
Leading foodservice provider Sysco Ireland has revealed plans to double the size of its Northern Ireland operation within five years
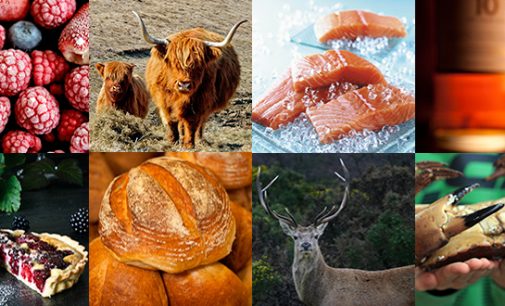
A project to create a food and drink technology centre in the Highlands has secured more than £3.2 million investment
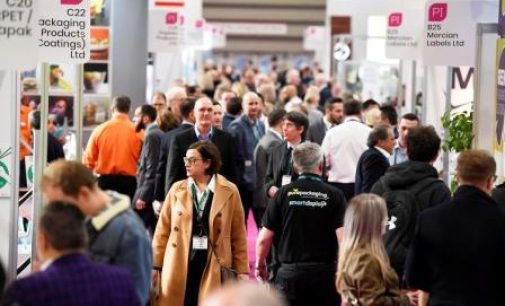
Packaging Innovations and Empack 2022 will introduce two brand-new interactive features, The Big Debate and the Sustainability Trail, when it returns
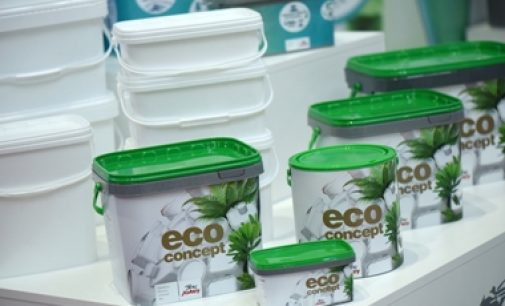
Sustainability, the packaging industry’s most contentious topic, is set to take centre stage at Packaging Innovations and Empack 2022, with the
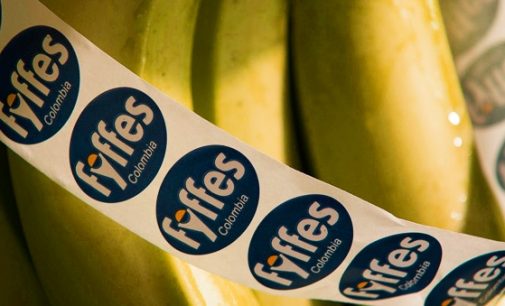
A new banana ripening and distribution centre, owned and operated by Irish banana distributors, Fyffes has opened and commenced operations
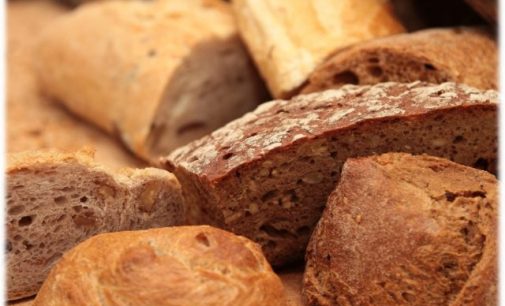
Gordon Polson, Chief Executive of the Federation of Bakers has written to the Rt Hon George Eustice MP, Secretary of
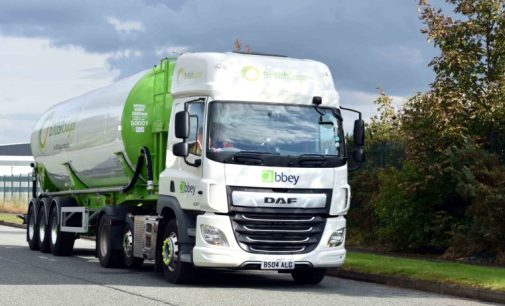
Bulk road tanker specialist Abbey Logistics has been awarded a new contract to transport all bulk flour produced at Premier
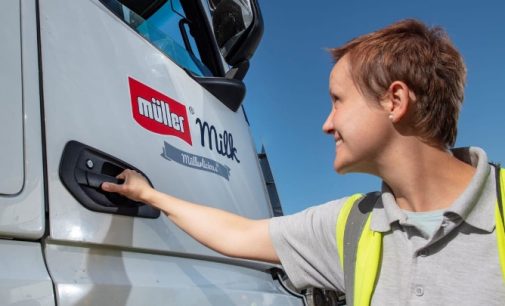
Müller Milk & Ingredients (MMI) has launched a significant recruitment push in order to maintain its first class customer service
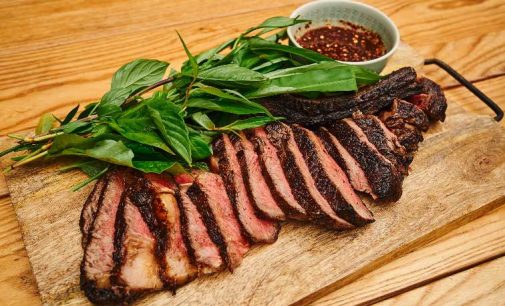
The Teagasc Future Beef Programme – Sustainable Cattle Production has been launched. The aim of the Future Beef Programme is
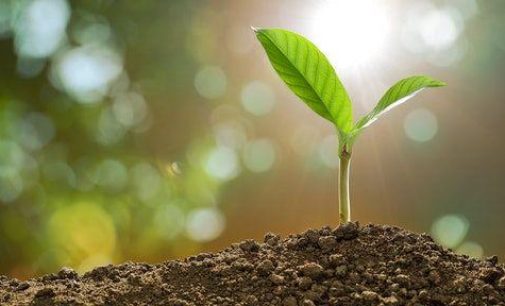
The global market size for controlled environment agriculture (CEA) is set to reach a market value of $100 billion by
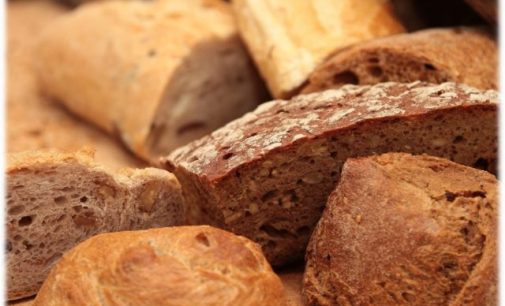
The Irish Bakery Association has warned that despite the best efforts of the industry, bread prices will soon be forced upwards
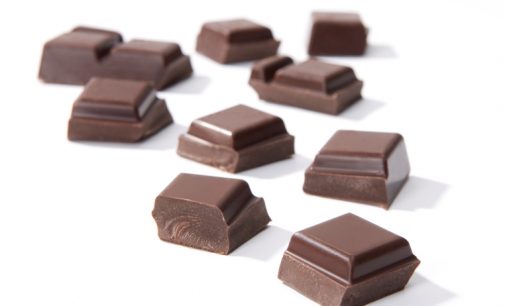
When it comes to cocoa and chocolate, sustainability is taking on increased importance, influencing consumers’ purchase decisions and their perceptions
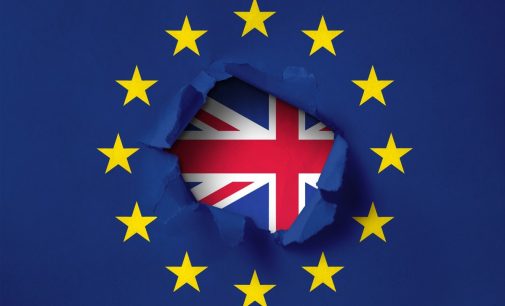
New research1 from Aldermore bank reveals that nearly half (47%) of SMEs who import goods and services from the EU
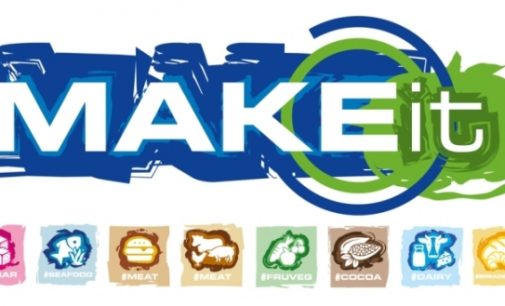
MAKEit, the EIT (European Institute for Innovation & Technology) Food project, has launched a new partner programme to accelerate research
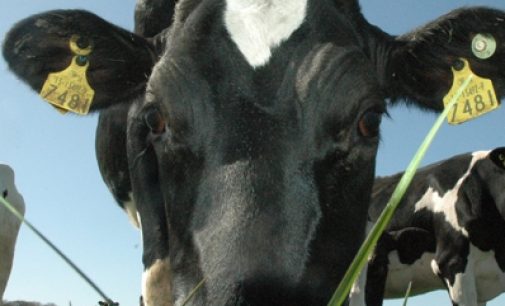
A new report on the Irish dairy industry and its position relative to a number of leading EU countries as
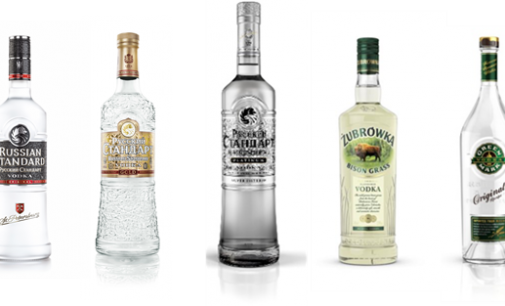
Since 2015, Roust has partnered with William Grant & Sons UK to manage the distribution of Russian Standard, Green Mark
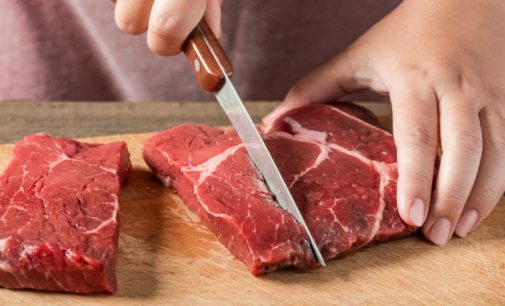
OSI Europe’s Operations Director and Head of Sustainability, Claire Donoghue, has been named Board Chair of the European Roundtable for
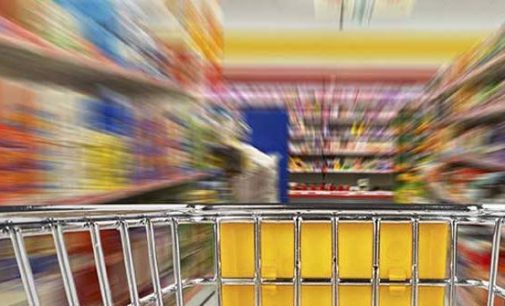
The UK food and grocery market is set to grow by 10% – or by £19.1 billion to £211 billion
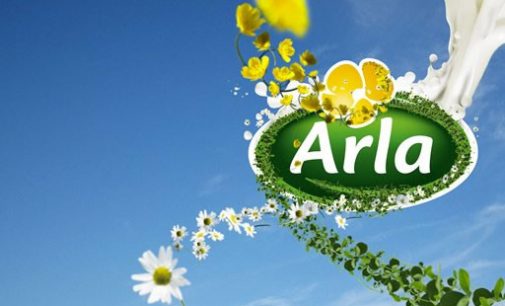
Arla Foods, the UK’s leading dairy co-operative, has announced a new partnership with the UK Centre for Ecology & Hydrology
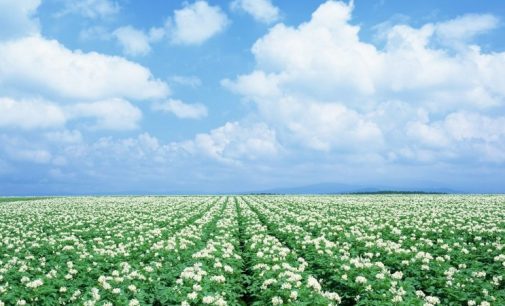
Starch Europe has welcomed the much anticipated publication of the European Commission’s EU Farm to Fork Strategy. Starch Europe and