Redefining Product Quality and Power Usage in Frozen Food Processing Plants
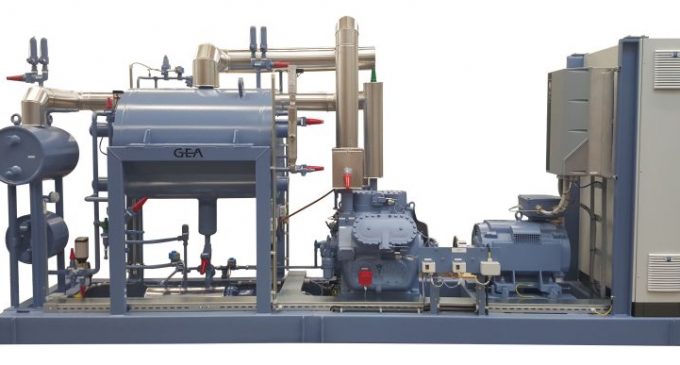
Every business wants to produce the finest quality products at the lowest possible cost. Every business wants to reduce energy consumption to save money and help protect the wider environment. The merging of two technologies from GEA, the S-Tec and A-Tec spiral freezer with CALLIFREEZE® and GEA heat pumps, is now enabling food processing companies to do both: enhanced quality and significantly more efficient use of energy in the plant.
Perfectly frozen products with CALLIFREEZE®
It was only a few months ago that GEA launched its new CALLIFREEZE® technology for its range of spiral freezers. CALLIFREEZE® ensures that all products are frozen precisely to the users’ requirements without wasting a single calorie of energy.
CALLIFREEZE® is a new inline freezer control system that’s exclusive to GEA spiral freezers. It calibrates the freezer parameters through the continuous measurement of the level of frozenness of the product at the freezer exit. GEA has enhanced its control system to continuously monitor the level of crystalized water in the products and adjust the retention time, air temperature and fan speed to achieve the precise level of freezing required, with the minimum of energy consumption.
Mathieu Nouhin, GEA’s Product Manager Freezing, said that there is no point in continuing to cool a product beyond 100 per cent frozen but, until now, there has been no way of checking the level of frozenness of products as a continuous part of the process. “CALLIFREEZE® uses GEA’s unique sensing and control technology to measure the level of frozenness of products exiting the spiral freezer,” he said. “It then adjusts the machine to achieve perfect freezing in line with the customer’s requirements.”
In one application for freezing breaded chicken, CALLIFREEZE® was able to reduce the retention time on the freezer from 85 minutes to just 70 minutes. This gave the company the opportunity of either reducing operating time or increasing production by approximately 20 per cent. In addition, the energy savings were in the order of 9 per cent on the refrigeration system.
Mathieu also explained that for several applications, 80 per cent level of frozenness at freezer discharge is acceptable with the product freezing being ‘finish off’ in the cold store for energy savings purpose. “The S-Tec, with CALLIFREEZE®, can do this too,” he said.
Adding heat pumps
The S-Tec spiral freezer, with CALLIFREEZE® makes a huge leap forward in energy conservation by itself, but when combined with the use of GEA heat pumps, the effect can completely transform the energy consumption of a plant.
Heat pumps recover the heat generated from refrigeration capacity produced for freezing or chilling operation, returning it to the plant to provide heat energy for processing, plant heating and hot water. They are very efficient, capable of generating three or four times the heat energy than, for example, electrical resistance heaters. In some plants it has been possible to totally eliminate the need for upstream boilers simply by reusing the heat generated in the down-stream chilling processes.
In use, the reduction in power consumption using heat pumps has been very dramatic. In one example at a food processing plant in the UK, power consumption at the plant was reduced by 68.6% with an associated lowering of CO2 emissions of 58.2%. The Return on Investment can be astonishing.
Kenneth Hoffmann, from GEA Refrigeration commented that processing plants often do not consider the use of heat pumps sufficiently early in their planning. “If they built in heat pumps to their design right from the start their power generation needs would be reduced and the plant design adjusted accordingly,” he said. “There is really no point in generating heat in one part of the plant and throwing it away in another. Proper use of heat pumps can avoid this.” Of course, heat pumps can also be retrofitted to existing plants to reduce energy consumption and still have a dramatic effect on overall efficiency.
Bringing the technologies together
The S-Tec and A-Tec spiral freezers, even before the introduction of CALLIFREEZE®, were market leaders for hygienic design and operating efficiency with pure horizontal airflow, a fully welded design to reduce dirt traps, and the flexibility to meet every customer’s needs.
By combining this market leading technology, with CALLIFREEZE® innovation, and GEA’s engineering ability to make full use of heat pumps to reuse energy and avoid waste, it is possible to completely redefine power usage within a plant and enhance product quality too.