Small Packs on Fast Flow Wrapping Lines: How to Comply with Weighing Legislations
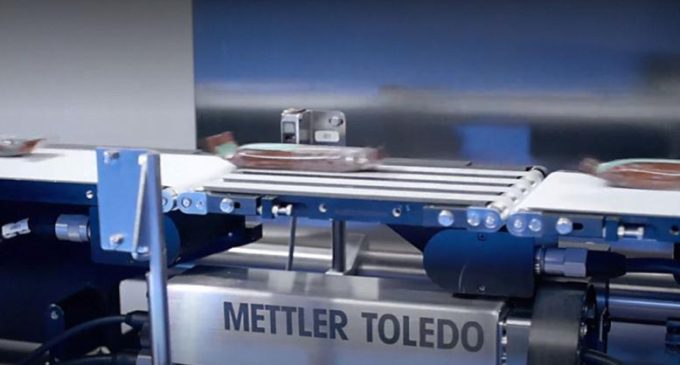
In modern food manufacturing, where speed and precision intertwine, those manufacturers navigating horizontal flow wrapping lines encounter a distinct set of challenges. As production accelerates to meet the demands of today’s market, compliance with stringent regulations for dynamic weighing becomes increasingly pronounced.
In this article, Frank Borrmann, Market Manager for the Strategic Business Unit Checkweighing, Mettler-Toledo Garvens GmbH, explores the world of small packs racing down the production line, offering insights and innovative solutions that resonate specifically with manufacturers in this swift and fast-paced domain.
Understanding the Regulatory Landscape
To select the most appropriate product inspection solutions, we must first navigate the regulatory landscape for pre-packaged goods, especially in high-speed flow wrapping operations. In Europe, Directive 76/211/EEC sets out uniform guidelines for pre-packaged products, addressing the complexities of compliance for manufacturers. The directive mandates adherence to the ℮ symbol conditions, signifying compliance with EU regulations on volume or weight marking. This intricate regulatory framework demands meticulous attention from manufacturers, influencing their approach to small packs on high-speed flow wrapping lines.
Similarly, in the United States, the NIST Handbook 133 outlines procedures for verifying the net quantity of contents of packages. Emphasising an effective testing programme, the handbook advocates for inspections at multiple levels, including point-of-pack, wholesale and retail testing.
Challenges at High Production Speeds
In food manufacturing, we continue to see increasing adoption of flow wrap machines on production lines. Flow wraps, ubiquitous in supermarkets, have become a staple in packaging various products, from bakery and confectionery to ready meals, primarily due to saving packaging material and the ability to produce foods at high speeds.
Adhering to the strict guidelines, while navigating the complexities of high-speed production lines proves to be a continual challenge for flow pack manufacturers. Compliance, alongside achieving consistent product weight, necessitates the importance of innovative solutions.
One of the inherent advantages of flow wrapping applications is the ability to create a seal that prevents the ingress of air into the packaging, helping to keep the products inside fresh and of a high quality. This dual advantage of high-speed flow pack machine capabilities and effective sealing has solidified flow wraps as a go-to-choice for manufacturers seeking both efficiency and product preservation in their packaging processes.
However, the faster and smaller or lighter a package is produced, the greater the need for more accurate in-line weighing. Challenges arise from the packaging itself, particularly the central edge of sealings, which can affect the stability of the product handling and weighing accuracy. In addition, shorter time available for measuring, challenging handling and sorting processes due to flow pack sealings, faster data processing needs and light weight products requiring smaller tolerances and higher accuracy all contribute to an intricate and challenging weighing environment.
As a result of these challenges, manufacturers are presented with two viable options for achieving compliance with food safety regulations: the traditional static scale or the advanced capabilities of a dynamic checkweigher. The choice becomes pivotal in crafting a robust quality assurance strategy for high-speed flow wrapping lines.
The Role of the Checkweigher
Checkweighers, in essence, act as guardians of compliance, meticulously verifying that each product racing down the line adheres to predefined weight or volume standards. They can serve as a last line of defence, preventing substandard goods such as single chocolate bars within a multiple pack, which did not meet the target weight, from entering the marketplace. As production speeds escalate, the checkweigher becomes increasingly crucial, offering a 100% automated in-line weighing solution to navigate the challenges posed by faster packaging and the production of smaller, lighter products.
Checkweighers also contribute significantly to proactive quality control. They act as a gatekeeper, detecting anomalies such as weight issues, that might escape human observation, including broken or missing components in products like chocolate bars. While manual inspections might fall short in revealing if a piece of chocolate is missing or broken, a checkweigher equipped with advanced features can astutely recognise if a piece is missing, due to its deviation in weight, adding a valuable layer of quality assurance.
Rising costs continue to pose challenges for manufacturers. Beyond obvious expenses, there are concealed costs associated with non-compliance with quality standards—rework, recycling, recalls, waste, manual spot checks and documentation. In this context, 100% in-line checkweighing is a cost-effective strategy.
To accommodate the space constraints of production line facilities, checkweighers are designed in a multitude of compact sizes. Integrating a compact checkweigher into the production line not only saves space but also offers seamless operation within limited spatial confines.
In response to food manufacturer’s needs, FlashCell™ loadcell technology from Mettler-Toledo, integrated on the C-Series Checkweigher, addresses challenges in handling small, high-speed packages. The innovative technology within the checkweigher incorporates a striped weighing belt to facilitate smooth product transfer. The use of energy-saving automatic sorters facilitate reliable rejection at the highest speeds while simultaneously contributing to a reduction in energy costs. Furthermore, there is no need for pneumatic infrastructure, normally required to operate with other sorting devices like pushers.
Beyond mechanical enhancements, the Mettler-Toledo C35 Checkweigher using FlashCell™ loadcell technology delivers superior performance. The integration of digital signal processing enables faster calculations, with a 33% increase in the sampling rate and a remarkable 400% boost in the Central Processing Unit (CPU) and Digital Signal Processing DSP algorithm. A notable addition is the advanced filter technology, which absorbs any disturbing frequencies therefore producing more accurate results. This cutting-edge technology excels at filtering out any disruptive factors, solidifying the checkweigher’s capability to provide precise and reliable measurements in high-speed production environments.
A dynamic checkweigher not only aids in compliance with weights and measures regulations, but also acts as a proactive solution to combat rising costs. The benefits span from reducing manual labour costs to minimising product waste, all while adhering to food safety standards and regulations, even in high-speed production environments. The two-fold approach of preventive and reactive maintenance further solidifies the role of checkweighers in offering sustained operational efficiency and cost-effectiveness.
We cannot discuss checkweighers and compliance though, without also acknowledging the importance of reject systems. Central to the compliance process is the selection of an appropriate reject system, be it air blast or pusher. The efficacy of the reject system is paramount in accurately identifying and removing non-compliant products, preventing substandard goods from reaching consumers. This becomes increasingly critical as production speeds escalate, demanding precision in every facet of the weighing process.
Conclusion
In an industry where precision is paramount and compliance is non-negotiable, the challenges of weighing small packs on high-speed flow wrapping lines are many. Checkweighers are not just a weighing solution, but a sophisticated and innovative ally, addressing regulatory demands, operational constraints, and the need for precision in an era of rapid production. As food manufacturers strive to combat rising costs and boost productivity, checkweighing technology offers efficiency, embodying the delicate balance between compliance and innovation in high-speed flow wrapping lines.
For more information on this topic, click here or visit www.mt.com/cw-flow-wrap-pr to register for an in-depth webinar on the 15th February 2024 at 8am and 2.30pm GMT.
About Mettler-Toledo C-Series Checkweighers
The Mettler-Toledo C-Series checkweigher, featuring the revolutionary FlashCell™ technology, represents a cutting-edge solution for precision weighing in the food industry. Designed to thwart the distribution of under- and over-filled packages, these dynamic checkweighers help products to meet stringent weight criteria. The range boasts exceptional reliability, contributing to compliance adherence and elevating quality control standards. Not only do these checkweighers minimise product waste, but they also conduct completeness checks for package components, enhancing overall product integrity. The system is adaptable, offering customisation options to seamlessly integrate with diverse production lines, facilitating trouble-free operations. With its high-performance capabilities, the Mettler-Toledo C-Series checkweigher, powered by FlashCell™ EMFR technology, offers maximum accuracy, making it an indispensable tool for challenging weighing applications.
For more information: www.mt.com/pi-precision-weighing