Ireland’s Deposit Return Scheme, Re-turn, has achieved a significant milestone, collecting over 20 million drinks containers since its inception on February 1. This achievement was reached on March 29. Re-turn recorded
Environment
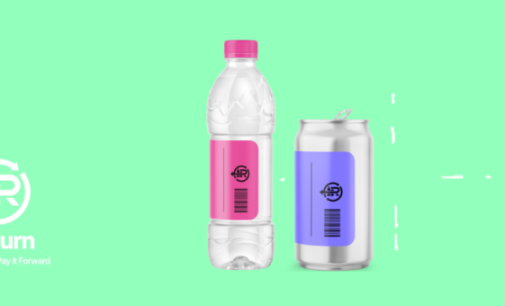
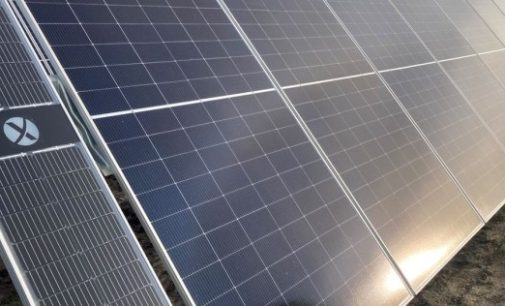
75% of the electricity now being used to make Britvic soft drinks in Great Britain – from Fruit Shoot to Tango, Robinsons to J2O – is coming from a 160-acre
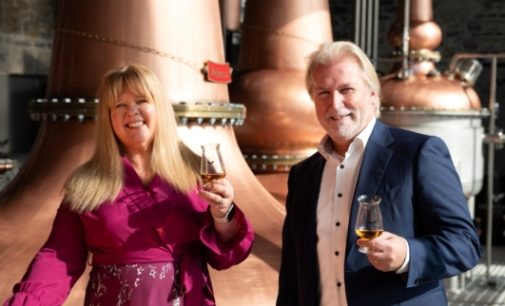
Ahascragh Distillery has been recognised as a verified member of Origin Green, Ireland’s national food and drink sustainability programme. The membership further highlights the distillery’s commitment to sustainable practices and
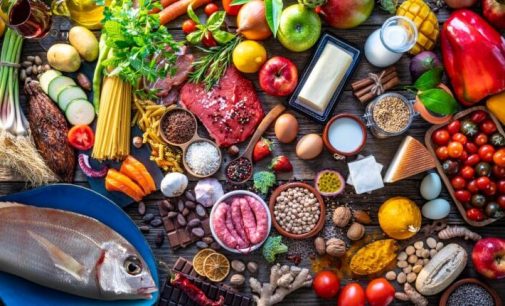
Innovate UK and the Biotechnology and Biological Sciences Research Council (BBSRC) are set to invest £15.6 million in 32 projects as part of the novel low-emission food production systems competition.
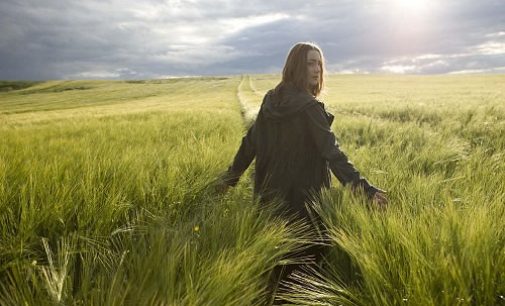
Bord Bia has acknowledged the sustainability performance of 97 Irish food and drink companies that have attained Origin Green Gold Membership in 2023. Gold Membership is given to companies, which
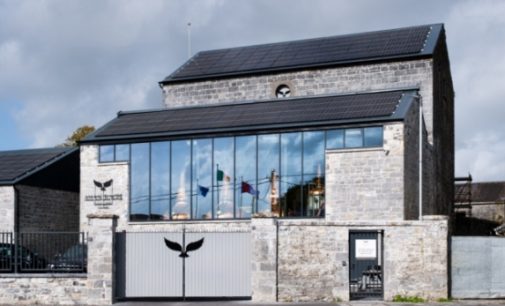
Ahascragh Distillery has taken home a prestigious award for the Innovative Deployment of Renewable Energy at the 2023 Sustainable Energy Authority of Ireland Awards. This accolade recognises the founders dedication
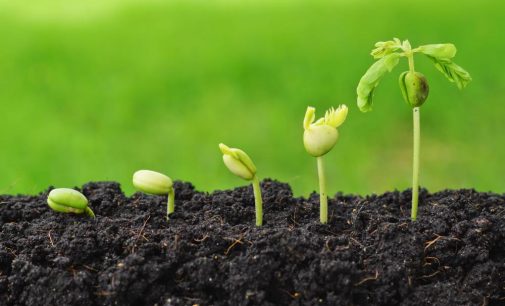
McKinsey & Company has released its latest insight on catalyzing a sustainable land use transition, revealing that 70-80Mha of additional cropland, equivalent to all of Brazil’s[i] cropland or 3x Tanzania’s[ii], will be
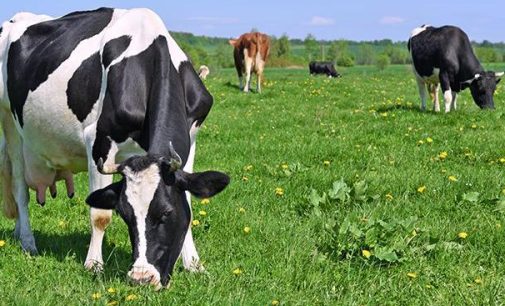
Dairy Industry Ireland (DII), the Ibec association representing the sector, has unveiled a new comprehensive report that highlights the substantial economic contribution, global market potential, and commitment to sustainable practices
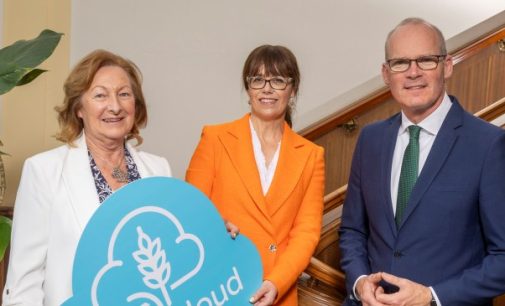
FoodCloud, a tech-based social enterprise which redistributes food which would otherwise end up as waste, has been awarded more than €500,000 research and development (R&D) funding from Enterprise Ireland’s Agile Innovation Fund to
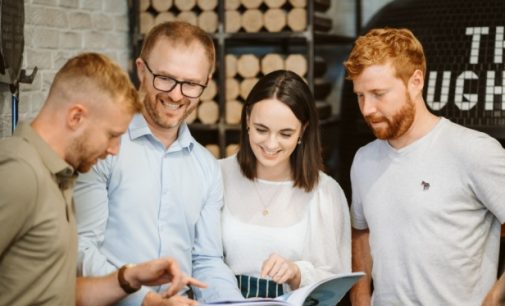
Ifac, Ireland’s farming, food, and agribusiness specialist professional services firm and a top 10 accountancy firm, has published its sixth annual Food and Agribusiness Report 2023 – the only report
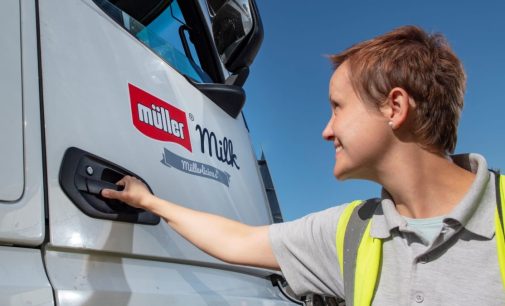
Müller Milk & Ingredients, which produces branded and private label fresh milk, cream, butter, milk drinks and ingredients products and boasts a network of dairies and depots servicing customers throughout
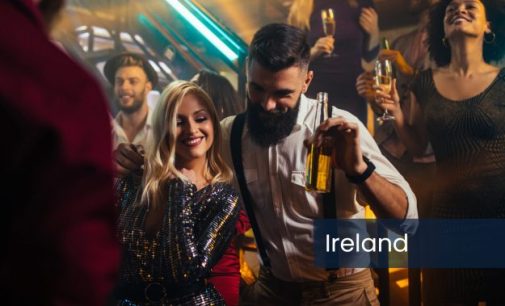
Sustainability and ethical practices have become key elements of consumers’ decision-making in Ireland—with crucial consequences for on premise businesses. According to CGA by NIQ’s ‘2023 Consumer Insights Report’, two in three adults
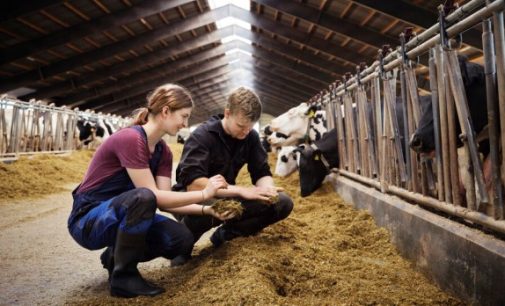
For the first time, Arla Foods has paid out a monthly incentive to its farmer owners’ milk price rewarding climate activities and other sustainability efforts being made on their farms,
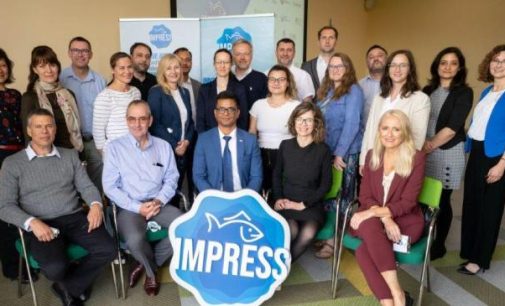
IMPRESS is an industry driven project, based on sound science and centred around the EU Bioeconomy and Blue Growth strategies, striving to promote sustainable and zero-waste production and consumption. The
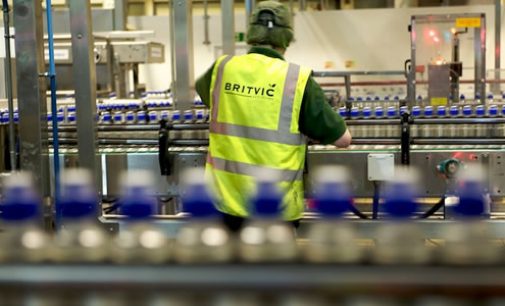
Britvic, the FTSE 250 global soft drinks business, has partnered with Atrato Onsite Energy, a leading solar energy provider, to deliver clean energy to Britvic via an innovative 10-year Power

The Scotch Whisky Association (SWA) has published a Water Stewardship Framework, offering research-based guidance for the Scotch Whisky industry as it works to improve efficiency and make reductions in its
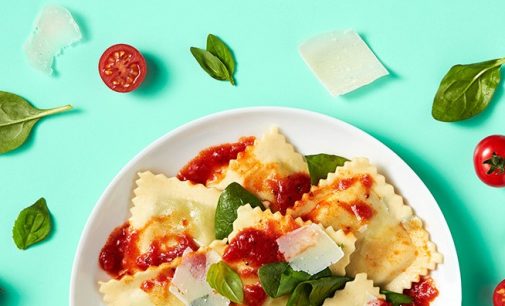
Bakkavor, the UK’s leading producer of fresh prepared food, is making progress on its efforts to reduce carbon emissions and food waste, as well as defining a roadmap to ensure
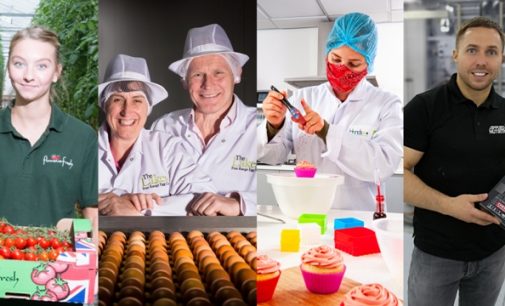
Made Smarter has launched a whitepaper to help SME food and beverage manufacturers accelerate their net zero plans. ‘Decarbonisation through Digitalisation: manufacturing made smarter and greener with technology’ is a
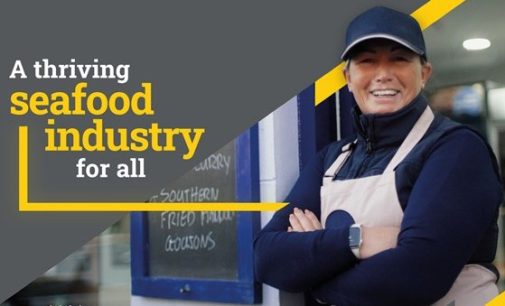
Seafish, the public body supporting the UK seafood industry, has launched its Corporate Plan 2023-2028. This strategic roadmap reflects the organisation’s vision for a thriving seafood sector and its ambition
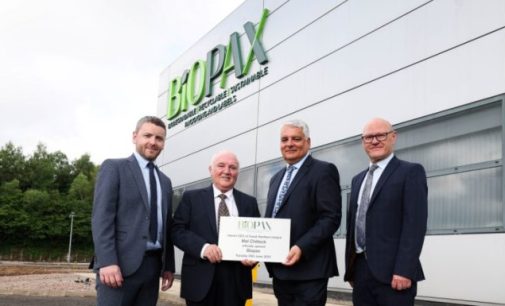
A new £47 million factory in West Belfast is set to revolutionise the FMCG and Foodservice packaging and labelling market with certified green solutions using the latest European, US and
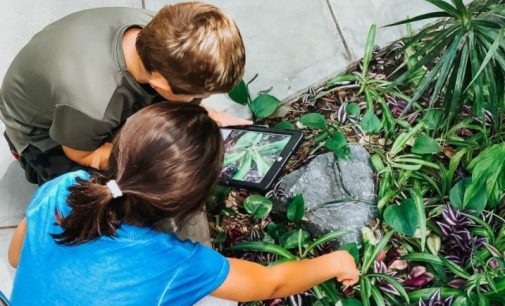
Innovate UK, the UK’s national innovation agency, has announced a new bilateral partnership with Protein Industries Canada (PIC), looking to develop greater connections between the food sectors in both countries
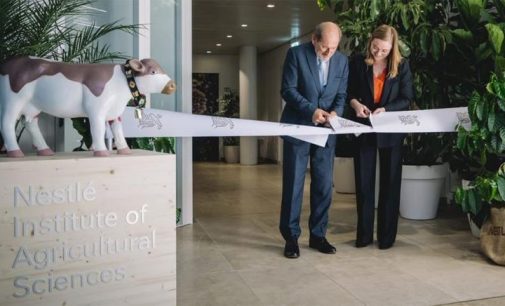
Nestlé has officially inaugurated the Institute of Agricultural Sciences to help advance sustainable food systems by delivering science-based solutions in agriculture. Speaking at the inauguration, Paul Bulcke, Nestlé Chairman, said:
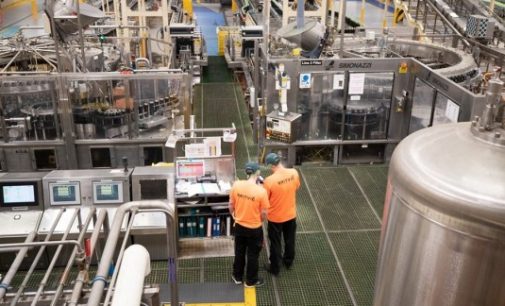
Leading soft drinks business, Britvic, is redoubling its efforts to cut carbon emissions and save energy – with £8 million
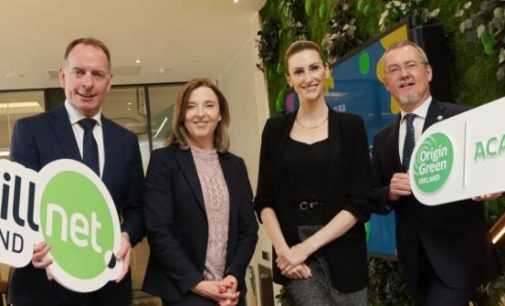
Bord Bia and Skillnet Ireland have launched the Origin Green Academy to develop sustainability skills and talent for the Irish
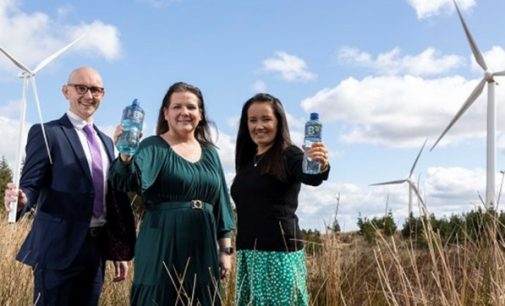
Britvic Ireland and Flogas Enterprise have announced a new Customer Corporate Power Purchase Agreement (CPPA) that will ensure that Ballygowan,
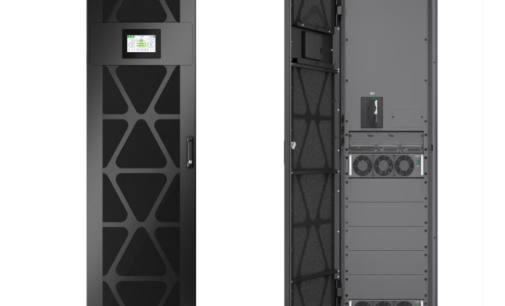
Modular design with Live Swap feature for small and medium size data centres and business-critical applications. 3-Phase 50-250 kW (400V)
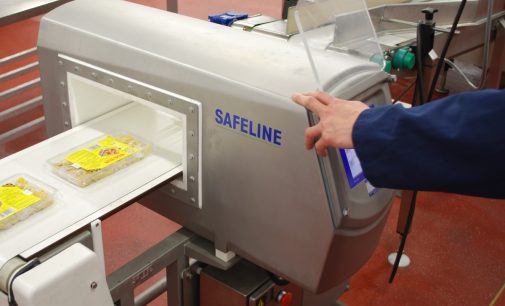
By Rob Stevens, Market Manager, Mettler-Toledo Safeline Metal Detection Retailers are increasingly including the requirement that food suppliers be able
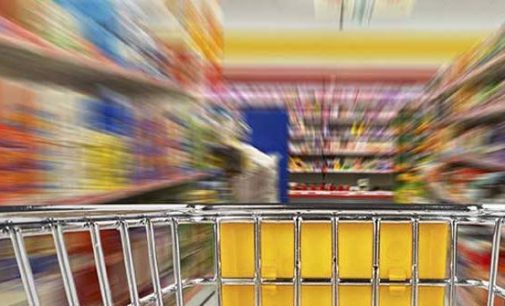
As part of the food and consumer goods industry’s shared ambition to halve the environmental impact of the UK packaging
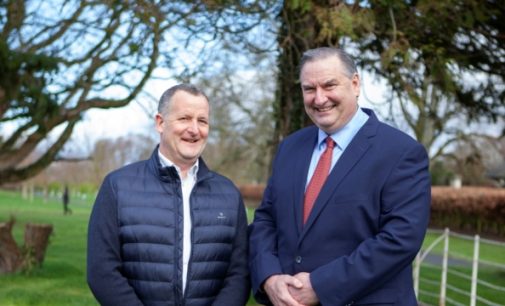
Irish-owned climate technology company ActionZero has announced a new partnership with one of Europe’s leading food companies. The Cork-based company

A new study by Bord Iascaigh Mhara (BIM) – the State agency that supports development of the seafood sector in
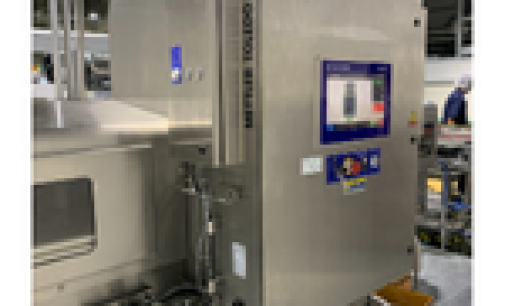
Live event scheduled 9th March 2023 will discuss the damaging nature of glass-in-glass contamination for food manufacturers and how x-ray
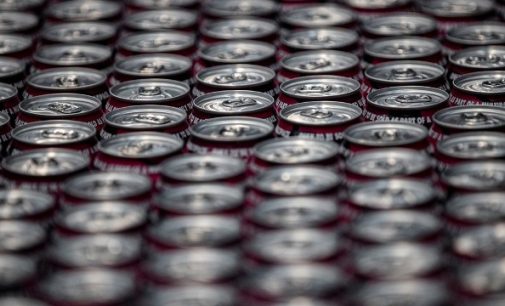
Drinks manufacturer Britvic has welcomed the Government’s announcement that a deposit return scheme will be established across England, Wales and
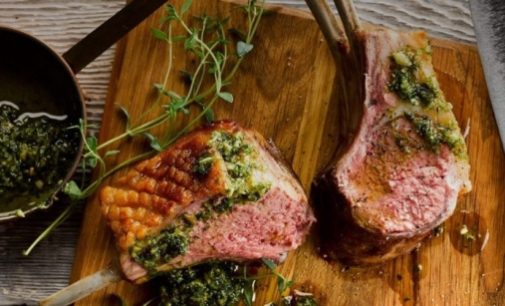
Dawn Meats has announced a substantial new plan which will see the Irish meat processor target Net Zero operational emissions
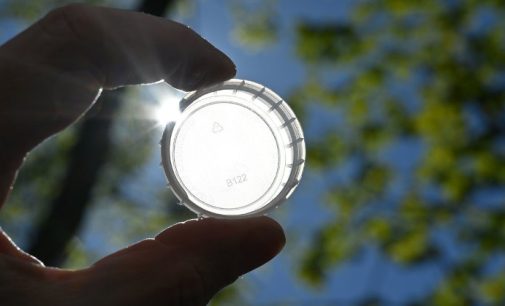
Following a series of successful trials, Müller Milk & Ingredients has started switching its coloured milk bottle caps to clear,
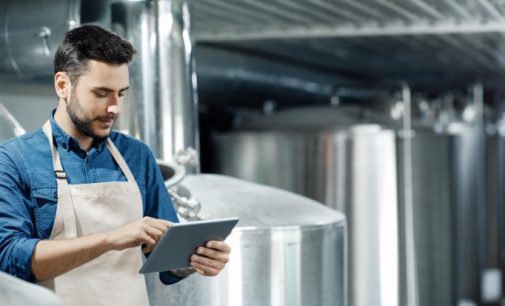
ABB has launched its ABB Ability™ BeerMaker intelligent process control solution to further support breweries in their operational efficiency through
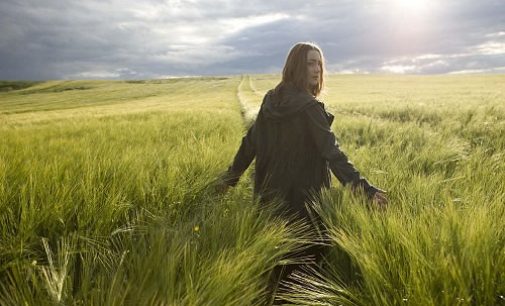
Bord Bia has appointed Emmet Doyle, from Cork city, as the first Bord Bia Organic Sector Manager. This is the
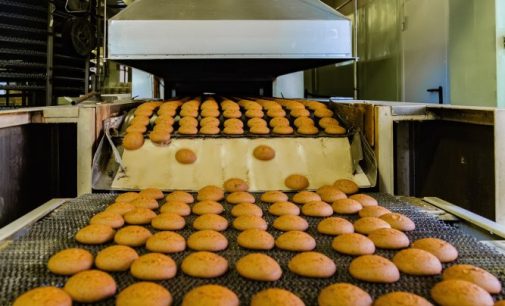
Nearly 50% of food and drink manufacturers have cut or paused investment projects as they face the toughest trading conditions
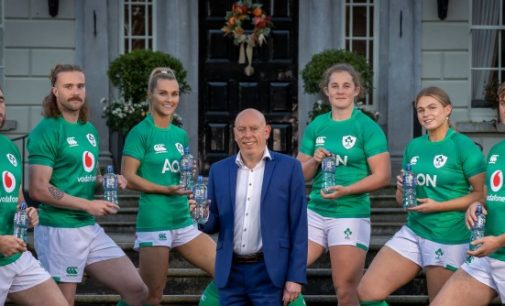
Ballygowan, Ireland’s number one water brand, part of Britvic Ireland, has been announced as the Official Water Partner of Irish
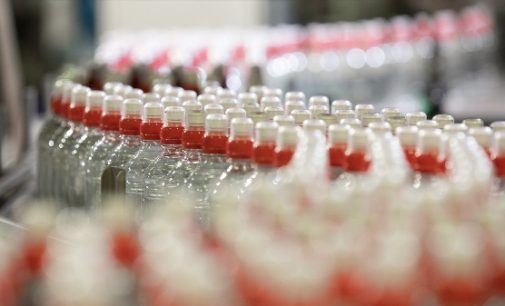
UK soft drinks manufacturer, Clearly Drinks, has announced that it has reached a key milestone in its environmental strategy, achieving
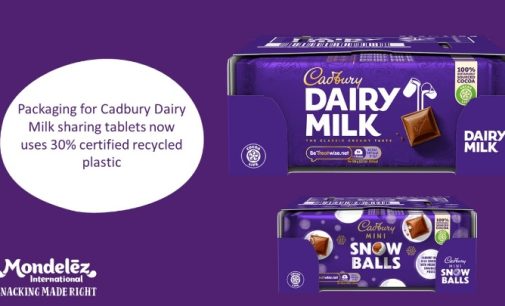
Mondelēz International has announced that its Cadbury Dairy Milk and Cadbury Mini Snowballs 110g sharing bars, which are made in
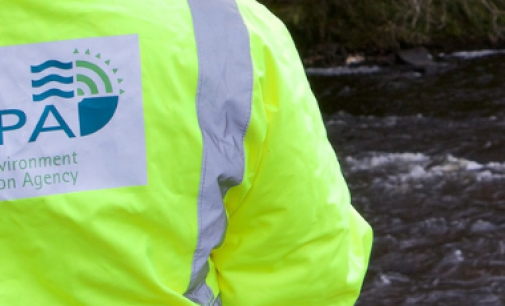
New, step-by-step guidance has been published by the Scottish Environment Protection Agency (SEPA) to ensure drinks producers are ready when
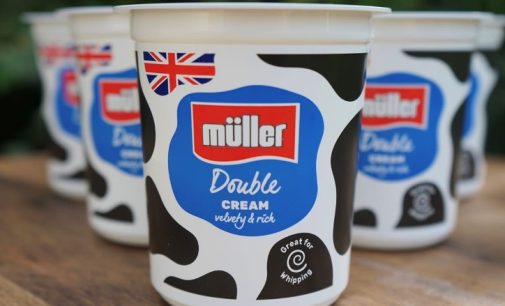
Müller Milk & Ingredients is to remove 500 tonnes of virgin plastic from its annual production of cream pots by
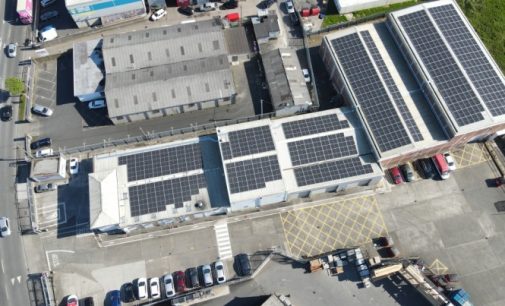
The Irish government recently announced ambitious new sectoral emissions ceilings, setting Ireland on a pathway to turn the tide on
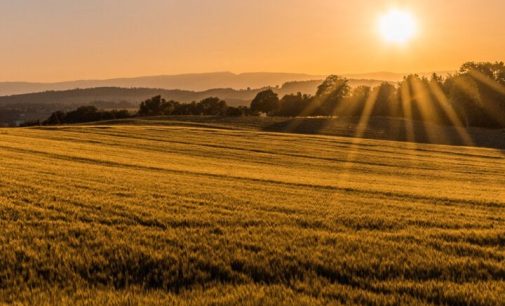
The Compleat Food Group (TCFG), the chilled prepared food processor, has launched a White Paper advising the UK Grocery sector
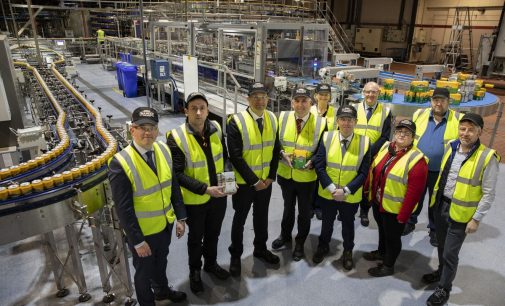
This project forms part of C&C Group’s broader ESG strategy and commitment to delivering to a better world. The Bulmers
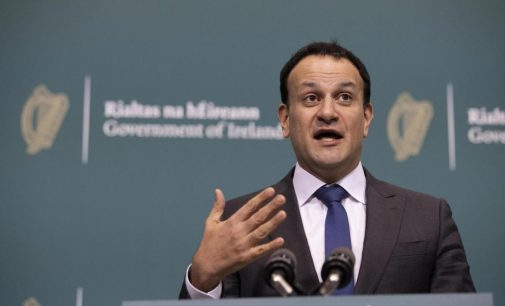
The Tánaiste and Minister for Enterprise, Trade and Employment Leo Varadkar TD, the Minister for Agriculture, Food and the Marine
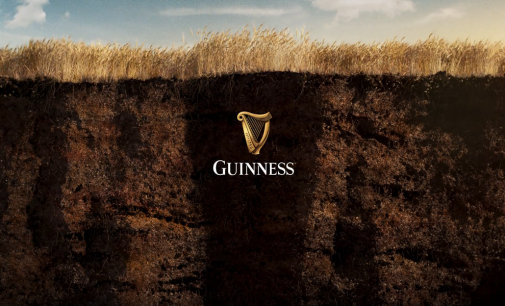
Guinness is undertaking one of the most ambitious regenerative agriculture pilots to take place on the island of Ireland. Regenerative
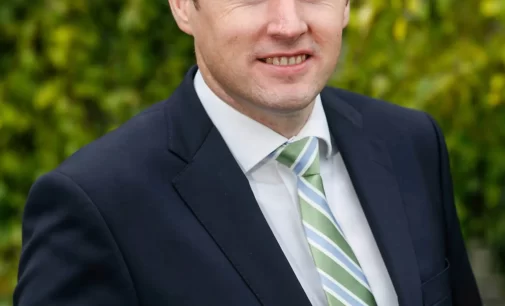
Ministers announce the commencement of payments to horticultural growers under the Horticultural Exceptional Payment Scheme Minister for Agriculture, Food and
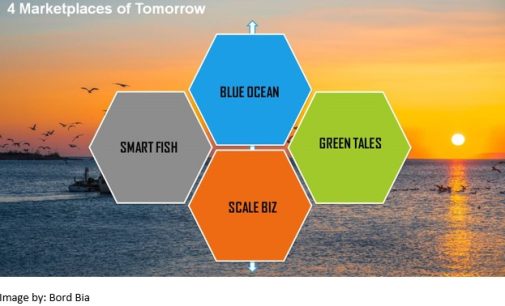
Bord Bia’s recently launched study, Seafood Futures: Four Marketplaces of Tomorrow explores what viable strategic choices will create the next
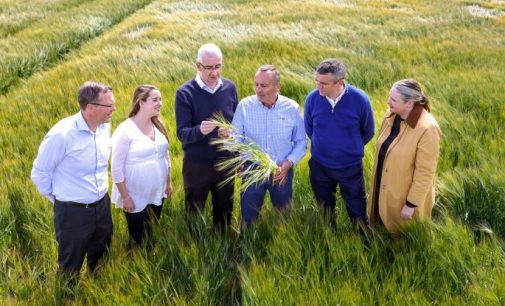
Diageo plans to invest €200 million in Ireland’s first purpose-built carbon neutral brewery on a greenfield site in Littleconnell, Newbridge,
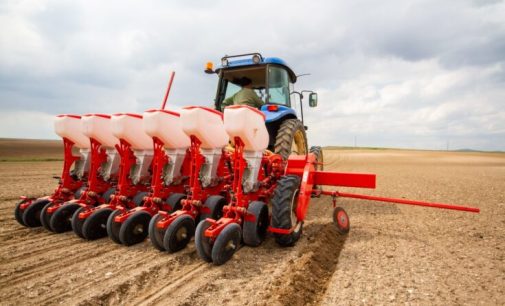
A novel network of researchers is set to help the UK’s agri-food industry move one step closer to net zero.
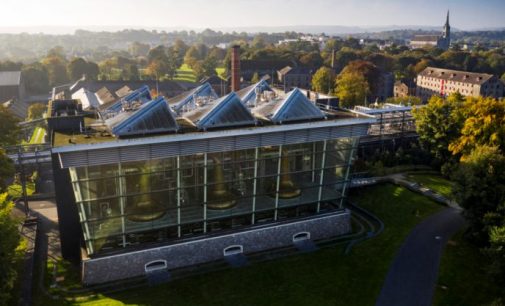
Irish Distillers will invest €50 million in its Midleton Distillery in County Cork over the next four years to deliver
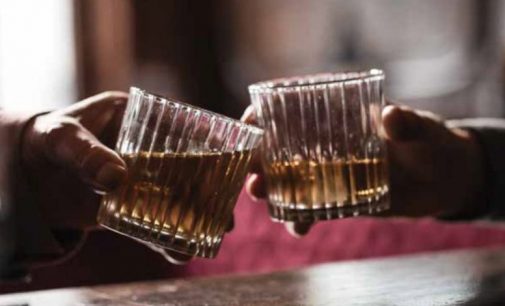
The Irish whiskey industry will lead the way in making Ireland the home of the world’s most sustainable distilleries and
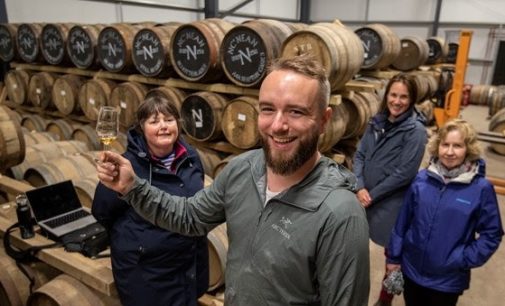
A project by a rural Highland distillery to reduce its carbon footprint while increasing productivity and creating jobs has secured