Alan Brown, site director at the McIntosh Donald factory based at Portlethen, Aberdeen, has been elected as Vice-President of the Scottish Association of Meat Wholesalers (SAMW) where he will work
End of Line
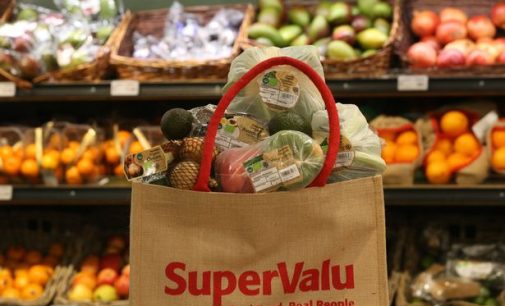
Musgrave Northern Ireland has announced today that the business has invested £3.2million in the rejuvenation of four SuperValu stores across Northern Ireland. The first of the four company-owned stores launched
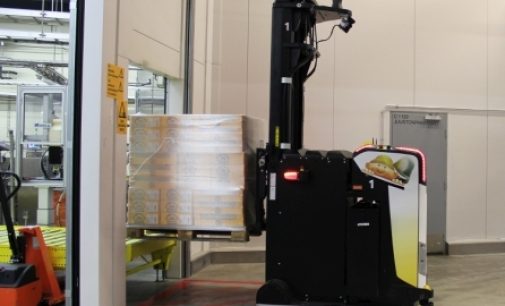
Valio is the leading dairy product manufacturer in Finland, and the Haapavesi plant processes and packs one of Scandinavia’s favourite cheese brands Oltermanni. Inside this factory there are two automated
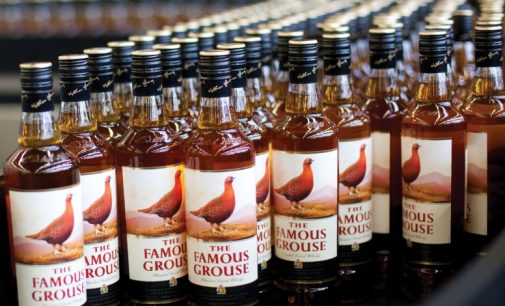
It’s one of the world’s favourite food exports and it’s important to keep the whisky flowing at all times. As the US writer, Mark Twain said: “Too much of anything
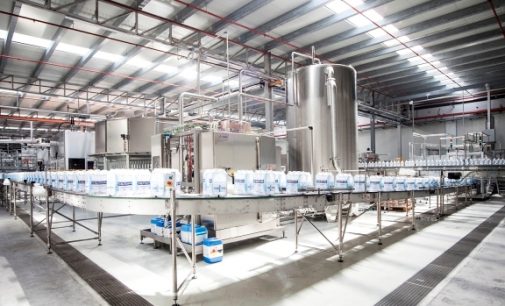
Lete is an internationally recognised trademark, thanks to the peculiarity of the naturally sparkling water and also because it is the main sponsor of Napoli Calcio. The collaboration with ACMI
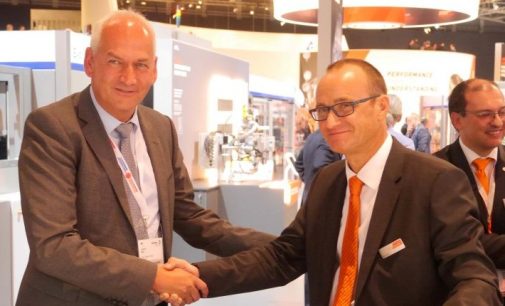
Gebo Cermex, part of the Sidel Group and world leader in packaging line engineering and material handling solutions, has recently signed a supply agreement with KUKA AG. Like Gebo Cermex,
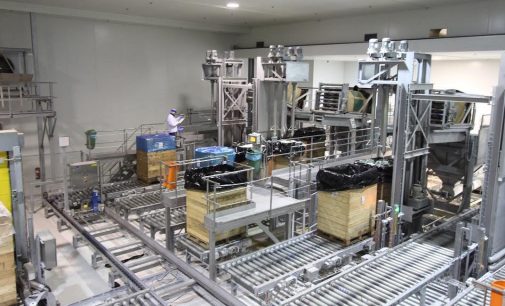
Bespoke design and automation of material pallet handling solutions and hydraulic elevators is the core business of Atelier Dumon. Atelier Dumon is a family owned company, based in Bruges, Belgium,

ACMI has installed in one of the South American plants of the Coca-Cola Femsa Group four PET lines of the latest generation each able to handle 12 different formats. Of

Tna has launched performance 5.0, a revolutionary new approach to high-speed production line performance ahead of this year’s interpack in Düsseldorf, Germany. Comprising a brand new high performance vertical packaging

Linerless gurus, Ravenwood Packaging has unveiled its latest game-changing technology, the VXR; combining vision, x-ray and seal check technology. The new innovation launched at Pro2Pac, ahead of the Ravenwood Annual

In recent weeks there has been some debate on the pros and cons of the cost of wrapping pallets from the point of view of just paying a cost per

The SSI Schaefer Group is the world’s leading provider of modular warehousing and logistics solutions. It employs over 8,500 people at its group headquarters in Neunkirchen, Germany, at its domestic

In the market for construction components, more and more gates, doors, frames and operators carry the Hörmann name, making Hörmann Europe’s leading provider of such products. This leadership of the

ASG Services – Labelling and Safety Solutions At ASG Services we have gained an excellent reputation for providing the most appropriate labelling and safety products to meet the specific requirements

Conveyor Systems Ltd offer an array of engineering expertise and a wealth of experience in materials handling solutions however complex, tailored to suit customer’s individual requirements in a wide range

ACMI project managed and installed at the French based Coca-Cola group in Socx-Bergues, a completely automatic end-of-line system to handle a number of different packaging solutions. Such a solution is
The trend for packages in the food and beverage industry towards the use of lighter and more delicate packaging materials is ongoing. This drives the need for new conveying solutions

Manna Foods is a producer of savoury sauces and employs 70 people. It is a family owned business, and although relatively small, they are extremely successful in what they do

Barry Callebaut, the world’s largest manufacturer of cocoa and chocolate products, recognised that a significant increase in operational efficiencies could be achieved through the installation of a robotic palletising system

PET solutions provider Sidel has created a new business unit to serve drinks products producers globally. Split into six teams including maintenance, line improvement, training, spare parts and logistics, line

“There are some important changes going on in the field of end-of-line palletising.” Jan de Bruijn, Managing Director at CSi’s Headquarters in Raamsdonksveer, knows that nowadays there’s a strong demand

UK robot sales figures for 2013 from the British Automation and Robot Association (BARA) reveal a 60% increase in robot uptake within the food sector, compared to 2000 results. With

Last year, LITA celebrated 50 years of activity and this important anniversary is evidence of the company’s efficiency and ability

FANUC Robotics UK has launched a new universal palletising robot that boasts best-in-class speed, payload, energy-efficiency and reach. The M410-iC/185
Valco Melton, as a leading manufacturer of adhesive dispensing and quality inspection systems for the packaging industry, offers a complete