Lidl GB has officially opened its £300 million RDC – the largest Lidl warehouse in the world – marking the discounter’s continued commitment to expansion across Great Britain. The 1.2
Automation
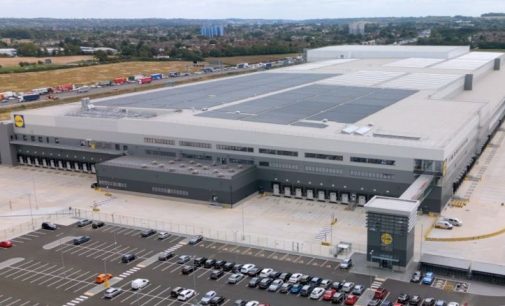
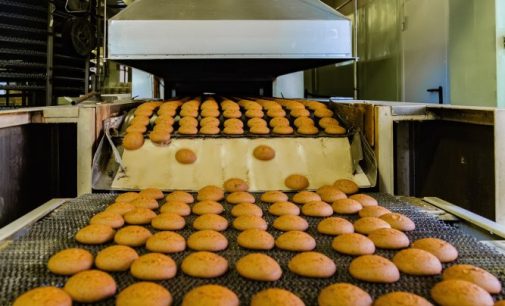
The Food and Drink Federation (FDF) has launched a new online platform to help manufacturers access the support needed to adopt innovation and increase their efficiency and productivity. The Food and
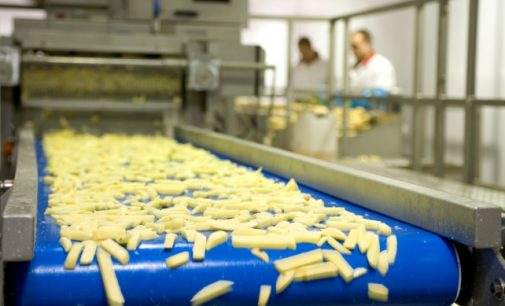
Food and drink manufacturers have helped Made Smarter’s pioneering technology adoption programme reach its 250th investment milestone. Among the latest businesses to secure support from the government-funded and industry-led initiative are:
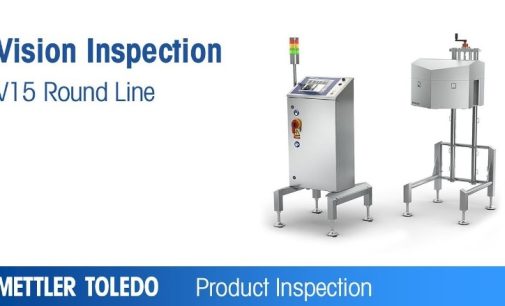
The German company Jürgen Langbein GmbH has been producing a variety of gourmet stocks, soups, sauces and pastes for more than 30 years at its headquarters in Kaltenkirchen, near Hamburg.
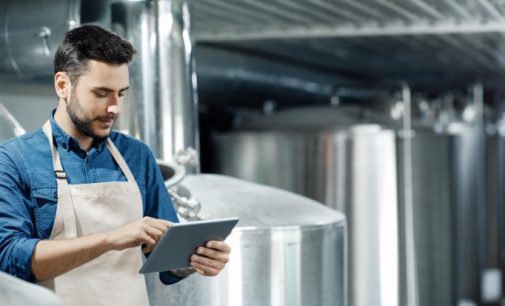
ABB has launched its ABB Ability™ BeerMaker intelligent process control solution to further support breweries in their operational efficiency through digital transformation. ABB’s brewmaster, who has the notable achievement of
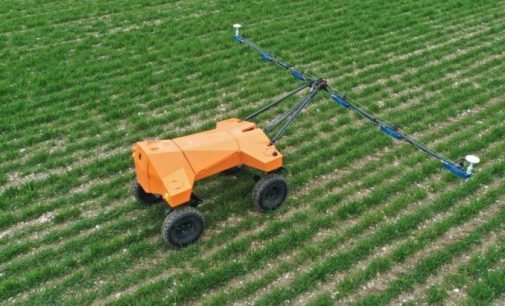
Small Robot Company (SRC), a British agritech start-up for sustainable farming, has launched its commercial Per Plant Farming robot services. Pilot trials this season have revealed herbicide applications can be
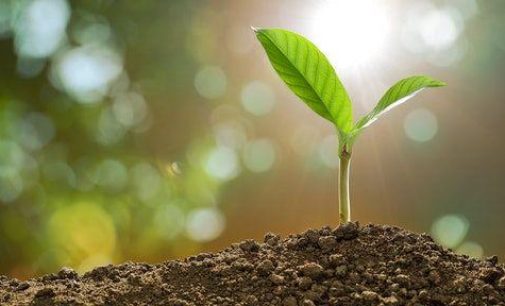
The global market size for controlled environment agriculture (CEA) is set to reach a market value of $100 billion by 2030, with six potential opportunities capturing $78 billion in market
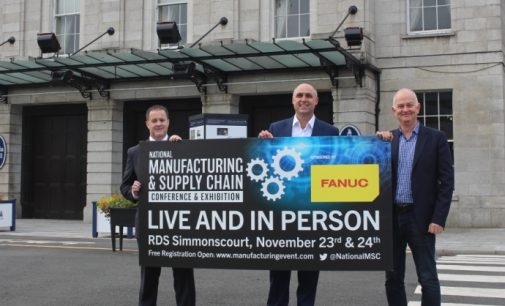
Following a period of unprecedented change and upheaval in the manufacturing and supply chain sector over the past 18 months the organisers of The National Manufacturing & Supply Chain Conference
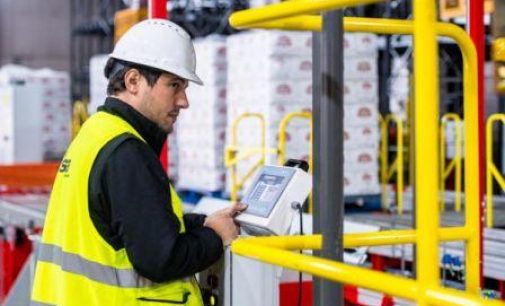
AB InBev is opening a new automated warehouse with space to store 23 million pints of beer at its largest UK brewery in Magor, South Wales. The world’s largest brewer
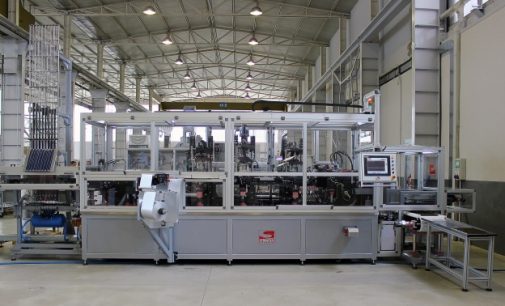
Spreafico Automation keeps growing, confirming its leadership position in the designing, building and marketing of automated machines and technologies for the filling of liquid food. In order to support the
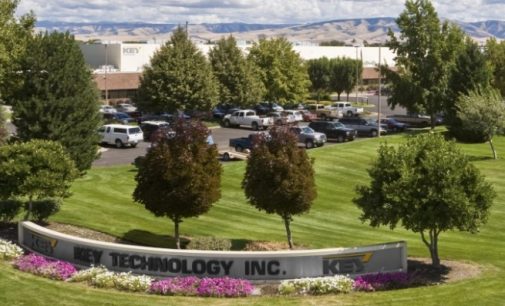
Key Technology, a member of the Duravant family of operating companies, is celebrating their 70th anniversary. Since introducing their first automated food processing system in 1948, Key has grown to
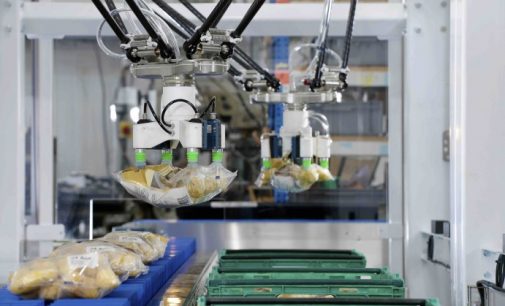
In food produce environments and packhouses, the benefits of automation when it comes to workforce health and safety are uncontended. From eliminating arduous and repetitive tasks to working uninterrupted within inhospitable
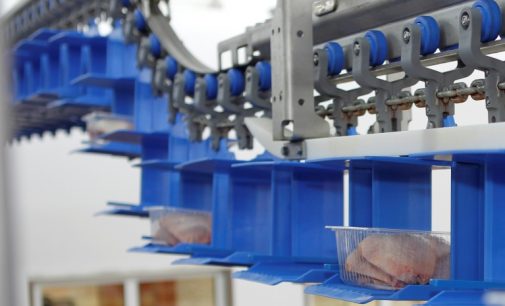
Once trays have been filled with product, poultry processors will often be faced with how to transport them to packaging equipment elsewhere in the plant. This job can be done
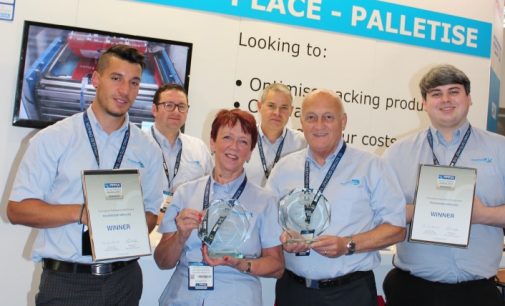
At the prestigious PPMA Group Industry Awards 2017, automation specialist Pacepacker Services repeated their 2015 success, winning two processing and packaging innovation awards. In addition to taking home the trophy
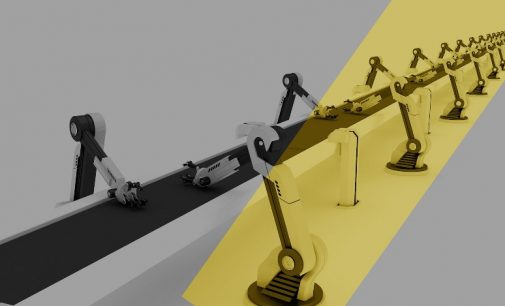
Zensar Technologies, a leading digital solutions and technology services company that specializes in partnering with global organisations across industries on their Digital transformation journey, has announced that 2 Sisters Food
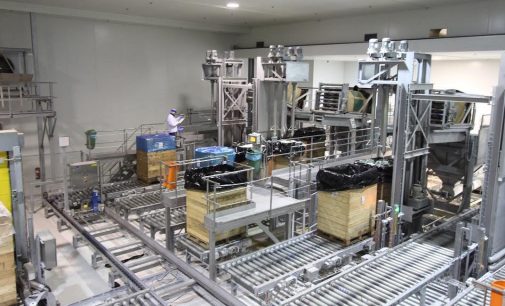
Bespoke design and automation of material pallet handling solutions and hydraulic elevators is the core business of Atelier Dumon. Atelier Dumon is a family owned company, based in Bruges, Belgium,
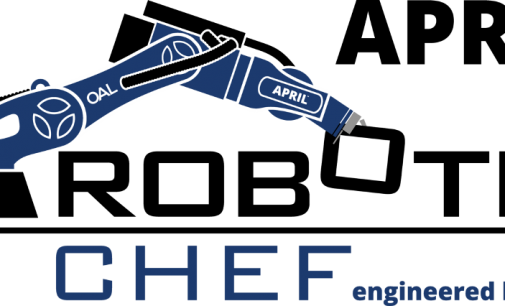
OAL Group has secured a £448,850 Innovate UK funded project to further develop its APRIL™ robotics material handling systems for food manufacturers. The new project focuses on overcoming the well

Breast cap deboning is an extremely important stage in any poultry processing plant. During this process, end products with the highest value, such as breast fillets and tenderloins, should be

Goliath Packaging Systems, in business since 2007, sources, supplies, installs & after-sales services a comprehensive range of End-of-Line Automation, Materials Handling & Industrial Washing equipment to the Irish Food/Beverage sector

Rising stars of the food industry saw and tasted the future when they visited the University of Lincoln’s National Centre for Food Manufacturing (NCFM) as part of their graduate development

Ichiban UK has invested in automation to ensure compliance with retailers’ codes of practice. The OAL system has prevented label and packaging errors that can result in substantial fines and

Heat sealing specialists Proseal has played a key supporting role in the development of the new production facilities at 2 Sisters’ Scunthorpe factory. The ambitious cutting and retail packing project

Pacepacker Services is teaming up with renowned equipment manufacturer and training provider Festo, to offer Automation Awareness Workshops for its

Earlier this year, Gemak was awarded a contract to manufacture and commission a state-of-the-art continuous yogurt processing plant at Llaeth

Conveyor Systems Ltd offer an array of engineering expertise and a wealth of experience in materials handling solutions however complex,

Gideon Hillman Consulting, established in 2004, is one of the UKs leading Supply Chain and Logistics Consultancies servicing it’s clients
AutoCoding Systems has recognised that there is a growing requirement to communicate with and collect data from a wide range
Robotics and automation has prospered in many manufacturing industries but there has been limited progress in food production because of

The second annual Food & Drink Business Conference & Exhibition will be held at the Aviva Stadium, Dublin on Wednesday,
Manufacturer of potato products and other frozen foods for the Swiss foodservice Enthusiastic chefs create from day to day the
Robots ensure efficiency and reliability Food processing places special demands on robot technology The world of robotics is currently facing

Whitefish processing is about to take a giant leap forward, with the launch of Marel’s FleXicut, a trimming robot for

Lamb Weston / Meijer, manufacturer of deep-frozen potato products and dried potato flakes, is investing 20 million euros in its

FANUC Robotics UK has launched a new universal palletising robot that boasts best-in-class speed, payload, energy-efficiency and reach. The M410-iC/185

At its recent 2013 Solution Partner Conference, Siemens awarded the accolade of ‘Best Factory Automation Partner’ to Autotech Controls. Autotech

On October 2nd 2013 Meyn officially opened its expanded Demo and training centre, when Scott Russell (Global Sales Director of Meyn)

Pacepacker Services has assisted a leading snacks manufacturer in increasing their output of packed crisp boxes with the installation of
Flavourfresh Solfresh group is one of the leading salads producers in theUKwhose business focuses entirely on the growing, packaging and
Dynamic Conveyor has released a new line of DynaClean conveyors, suitable for food processing operations. Manufactured using high density polyethylene

Within any business, finding a like-minded supplier can be a recipe for success and in the case of Ridgeview Wines,
Companies in the food processing and production industry thatstruggle with tough and re-occurring problems can increase productivity, and save time

Robotic packaging line manufacturer, TekPak, has recently launched an innovative pick and place case packer which is described as a

An automated packing line, installed by Endoline Machinery, which erects and seals cases containing up to 26,000 bottles of wine
Continuing increases in demand, along with the obvious need to remain competitive, led Birtwistle Catering Butchers, a fourth generation family
Idhammar Systems, leading provider of lean manufacturing and maintenance software including CMMS and OEE systems announced the launch of their
When Gerhard Schubert presented his first hot-melt box erecting and gluing machine to the public 46 years ago, his sons
16 Marel OCM9500 Box Labellers deliver consistent weighing accuracy at higher speeds than manual labelling and reduce manning levels on
Ishida Europe has developed a versatile mix-weighing solution for Benelux frozen snacks market leader Ad van Geloven for the introduction
Sensing solutions specialist SICK UK is hitting the road with a series of its popular Technology Days to bring expert
The UK’s leading people management standard, Investors in People specialises in transforming business performance through people. The Gold standard is
Egemin has signed a contract with La Costena, a Mexican producer of canned foods. Egemin is to install a new
New to the Marel range, the WPL9010 Manual Weigh Price Labeller is ideal for low volume labelling of individual packs,
London – That automation can protect, rather than destroy, jobs by improving the productivity, competitiveness and skills base of UK manufacturing,

The world’s first commercial robotic milking rotary has been unveiled by Swedish dairy equipment company DeLaval at a pilot farm