A Robust New Standardizer From Tetra Pak Makes Life Easier For Dairy
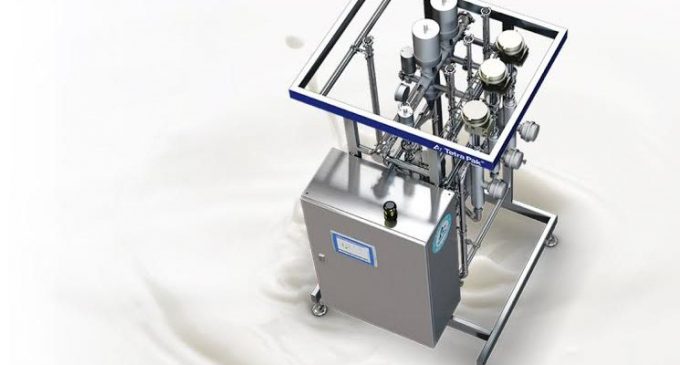
Producing standard white milk is a low-margin business. It is vital to produce milk with optimal fat content to get the most out of every drop of milk. That is why the standardization of milk is such an indispensable process. At Arla Foods’ dairy in Palmers Green, London in the United Kingdom a new Tetra Pak® Standardization unit makes that process more reliable, stable and accurate than ever before.
Josette Bogerman, Regional Project Manager at Arla Foods, says the cooperative had to replace three obsolete standardizers. “Then we heard about the new equipment from Tetra Pak,” she says. “It was perfect for us to try a new unit at that point in time.”
Arla Foods’ requirements were to minimize the downtime to three days. “That is exceptional for us,” she says. “I love working with Tetra Pak. They gave us the right guarantees. We would never have had the commitment from anyone else to do it in three days.”
Automatic In-line Standardization
By October 2015 Tetra Pak had installed the brand new version of the Tetra Pak Standardization unit at the Palmers Green site and the field test of the machine could begin. The standardization unit is designed for automatic in-line standardization of the fat content in milk and cream directly after milk separation. It is a highly reliable system based on extensively tested and refined automation software and high-performance, high-quality components such as flow transmitters and regulation valves.
“As for reliability – we haven’t seen it down – it’s always running,” Bogerman says. “We had a single issue and Tetra Pak dealt with it within the same day. We suspected we would have problems, since it was a field test, but it’s been a valuable experience for us.”
When Arla Foods runs a milk recipe with the milk fat set point of 3.0 % the standardization unit delivers a fat content of 3.0 % +/- 0.015 %. Says Bogerman: “We can see the difference in higher accuracy, a lot of cream is coming back into our tank. For every single batch we do, accuracy is improving.”
Stability
The equipment’s stability was one of Arla Foods’ main criteria when making the purchasing decision. The machine runs at least eight hours a day, seven days a week, all year round. “Our operators favour the new machine when it comes to short runs, since they are difficult to standardize,” she says. “It is so much more accurate. There was no choice. We had to have it. Life is much better for the operators.”
Before, Arla Foods had problems with in-tank standardization. Based on the experience of the operator, a sample was taken from the tank and the fat content was adjusted accordingly. “That has very much changed. Now we always know what’s in the tank. Our operators trust that what they read on the screen is going in the tank. Greater accuracy has started to save us money,” explains Bogerman.
Winning or Losing
In the highly competitive dairy market an efficient standardization of fat in the milk is a matter of winning or losing. “We have such a low margin on fresh milk,” Bogerman says. “For us, the big money is in cream. We can’t afford to produce milk with too much fat in it due to operator errors. To give cream away is an absolute no-no.”
The Palmers Green dairy processes about 1.2 million litres a day. A robust standardizer has become more and more important as the number of products has increased. “Different customers demand that their milk to be processed separately,” says Bogerman.
“We deal with enormous amounts of product changes and segregation. That gives us much less time for standardization in the tanks. We can’t wait to buy more and replace the other two standardizers,” she says.
Main Benefits With the New Solution
- Highly reliable system – based on extensively tested and refined automation software
- Maximum line utilization – with virtually non-stop production, thanks to fast, sophisticated algorithms
- Automated measurement and control of process variations — keeps you on target to secure uniform product quality
- High-performance, high-quality components make the system setup very robust
- Performance guarantees on precision: +/-0.015% 24/7.