Could Water be the Source of Energy Savings in Food Processing?
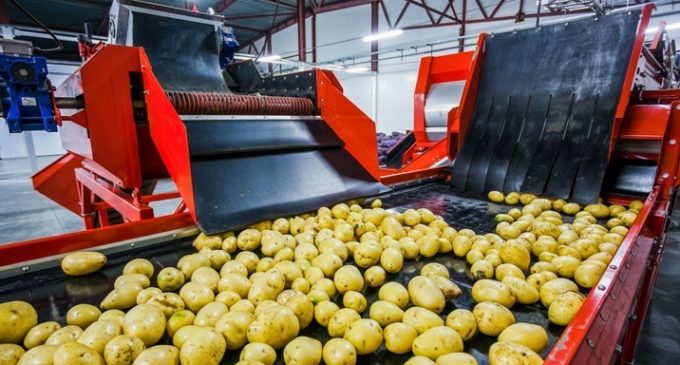
By Gary Sewell, General Manager, Clearwater Technology
Cost reduction is a constant challenge for any food processing business, yet many fail to realise the benefits that optimised water consumption can have on their overheads. Through investment in the right water treatment technologies, food processors can significantly reduce water consumption which can impact hugely on their utility bills.
Water, electric and gas are the main contributors to the overall expenditure of the business operation which set the base for the cost per kilogram of product produced, therefore employing a proven technical approach to water usage optimisation can drastically reduce utilities expenditures as well as carbon footprints.
Water treatment technology can be applied to reduce both influent and effluent water consumption, providing businesses with a reduction in cost per kilogram of product, thereby offering a strong competitive advantage. For businesses obliged to meet greener standards from customers, governments or trade associations, it brings the peace of mind that those standards can be more easily met.
By assessing each application in which water is used, food processors can develop a deeper understanding of where, why and how their water consumption can be optimised, ultimately making their dependence on water friendlier to both the environment and the bottom line.
Feeding the Process
Sourcing water from the local water authority, businesses are permitted to purchase a limited quantity of water within a specified time frame. Often this is extremely difficult to comply with and various methods of water storage are required to buffer the situation, yet these aren’t often effective enough. If the operations that rely on that influent water are not completed within the given time frame and water capacities become depleted, it must be sourced elsewhere.
For many businesses, borehole water is the best solution and probably the cheapest option. However, water treatment is essential to ensure it is compliant with water regulations and fit for purpose, especially if it is to be used as part of the process or product. The filtration and disinfection of borehole water can be completed efficiently with chlorine dioxide generation systems and the correct pre-treatment. Some processes may also require reverse osmosis or re-mineralisation depending on the application.
To make the process of sourcing and treating borehole water cost effective compared to additional pre-treated water from the local water provider, the right technologies must be applied. All too quickly, the costs of implementation and treatment can add up, but an experienced water technology provider with the right expertise can ensure that a cost-saving solution is tailored to the business’ unique requirements.
Analysing the Processes
Once influent water is of usable quality, its intended usage must be analysed. Common food manufacturing processes such as steam cooking and steam boiling require processed water to be treated to a quality that avoids scaling within the industrial and process equipment, reducing the costly requirement to clean, service, repair or replace equipment, while meeting hygiene standards.
It is then important to look at the amount of energy required to create the steam. Through analysis of a typical water treatment and pre-treatment program, the cycles of concentration in each boiler can be optimised to reduce the amount of water required to maintain a constant steam load. This is achieved by integrating a turn-key pre-treatment plant designed specifically to reduce the amount of water having to be blown down the drain to prevent deposition. This removes the requirement to replace the water that has been blown down the drain and can save in excess of 5 percent of energy expenditure. This also reduces the amount of waste water, helping businesses achieve a direct reduction in energy usage and a reduction in the total cost of operation.
Cooling towers are another common area where measurable savings can be achieved. The quality of make-up water can be optimised through treatment, but the system must also be analysed for losses and leaks. Within the Food and Beverage industry, losses and leaks are rarely managed for optimisation and can often result in as much as a 33 percent water saving.
The fans and recirculation pumps used to cool the water within the towers can also be replaced with more energy efficient solutions that allow water to be recirculated at a desired rate rather than a constant which is typically the norm and often results in water returning and overflowing the cooling tower base holding tanks. As part of water saving optimisation, systems have been developed to capture and re-use a portion of the bleed water from cooling tower systems which further improves their operational efficiency.
Optimising With Expertise
Selecting the correct water technology provider to apply the most suitable solutions is critical to achieving the goal of reduced water consumption. The right provider will be able to highlight key areas in which savings can be achieved such as energy, chemicals and equipment, otherwise it cannot deliver true ROI.
The service provided must be tailored to each unique business case in order to guarantee that the water treatment solutions are both economical and effective. After sales care is equally as important and regular service visits will ensure that water consumption not only remains cost effective, but can be further optimised in response to future developments.
By implementing the correct water treatment technology, it is clear that energy costs can be reduced by optimising both influent and effluent water across food processing.