Thirsty Business – How Water Reuse Can Benefit the Food and Beverage Industry
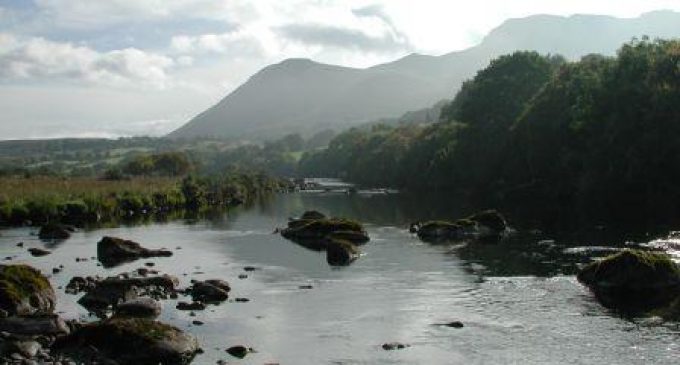
By Martin Kunz, EMEA Segment Leader, Industry with Xylem’s Applied Water Systems business
Only 2.5 percent of the world’s water is fresh water, and of that, only one percent is accessible as much is trapped in glaciers and snowfields. By one estimate, global fresh water demand will exceed supply by 40 percent in 2030 if current trends continue. As a result, water reuse is at the forefront of how businesses can expand sustainability efforts and mitigate business risk by lessening dependency on external water sources. Many companies realize substantial cost savings from water-related investments. There is also greater focus on social responsibility and water stewardship. All of these factors are increasing water reuse globally.
There are a wide variety of technologies commercially available for wastewater treatment in reuse applications. These technologies can be classified as conventional treatment processes, which can remove solids, and adjust pH and chlorine levels, or advanced processes, which filter and oxidize water resulting in a higher quality product.
A conventional treatment process removes solid waste found in water. These technologies provide minimal disinfection and include the use of screens, dissolved air flotation and primary clarifiers, filters, biological treatment via conventionally-activated sludge, chlorination and pH adjustment, reducing solids and Biochemical Oxygen Demand (BOD). For some reuse applications, such as turf irrigation, conventional treatment may be all that is needed.
Advanced treatment technologies go further to remove contaminants including:
- Solids and bacteria via microfiltration or ultrafiltration membranes.
- Biological nutrient removal with sequencing batch reactors or membrane bio reactors.
- Dissolved organics or salts with reverse osmosis.
- Trace contaminants and pathogens via oxidation and disinfection.
- Dissolved organics and contaminants via an adsorption process or ozone-enhanced biological active filtration.
Advanced treatment processes can be broken down into two categories: biological and disinfection. Within biological treatment there are two subcategories: Sequencing Batch Reactor (SBR) and Membrane Bio Reactor (MBR). Generally, SBR will have lower capital requirements than MBR, but MBR systems will cost less to operate. They combine biological treatment with membrane filtration to provide a high quality effluent, meet stringent nutrient limits for phosphorus and nitrogen, and have a smaller footprint compared to SBR technology.
Disinfection treatment comprises chlorine, ultraviolet (UV) and ozone treatment. The most basic form is chlorine disinfection where water is filtered with hypochlorite to generate chlorine residual that inactivates pathogens such as bacteria. UV technologies are chemical-free and require less contact time than chlorine disinfection. Water is channeled through a reactor that emits UV light at low wavelengths to destroy the DNA structures of microorganisms, including bacteria, viruses, yeasts and molds. Virtually any liquid can be used with this technology, so it is often found in beverage-processing plants; however, UV is sensitive to the clarity of the water. Higher clarity water requires less energy to treat, and, as a result, pretreatment of wastewater is common in systems where UV disinfection is used.
Ozone and Advanced Oxidation Processes (AOP) are powerful oxidation treatment technologies that generate hydroxyl radicals, the strongest oxidant used in water treatment. AOP is an ideal disinfection approach to treat recalcitrant contaminants that are otherwise not removed by other technologies. AOP and ozone technologies are commonly coupled with other filtration technologies.
In addition to the biological and disinfection techniques presented above, there are other advanced treatment technologies that can be used either separately or in conjunction to fulfill wastewater discharge requirements.
Membranes
Membrane filtration, using technologies such as microfiltration and ultrafiltration, provides suspended solids removal found in the processing of foods and beverages. These technologies can remove some pathogens, viruses and bacteria.
Reverse osmosis (RO)
In reverse osmosis, salts and many dissolved organics are removed through a semi-permeable membrane. RO is used when the highest quality reuse water is needed, such as high-pressure boiler feedwater or any use where low salt and contaminant levels are required. RO can be expensive and generate a concentrate brine waste stream that must be managed via proper disposal.
Pumping systems
Treating water is only the first step to ensuring wastewater is recycled and reused efficiently and effectively within a plant. It is important for organizations to also consider the transportation and storage required for water reuse.
Treatment and pumping systems are primary energy consumers within a water or wastewater loop. Sizing the system and selecting the right equipment to meet specific reuse requirements are critical to maximizing energy savings over the life of the equipment.
Pumps serve two purposes in a reuse system: transporting and pressure boosting. Water needs to be moved from one location to another for treatment, storage purposes, or for use. Pressure boosting is required for some treatment technologies, including RO, where specific pressures are required to move water through a membrane. Many reuse applications, such as irrigation and equipment washing, also require boosting capabilities.
Selecting the right pump
The pump and piping selection can have a considerable impact on the energy consumed over the course of the system’s life. Pumps should be selected to operate at their Best Efficiency Point (BEP) and the plumbing should be engineered to minimize friction loss. Xylem estimates that a water reuse system using incorrectly sized piping and pumps can increase energy consumption by 200 to 300 percent.
Implementing a water reuse system
- Define objectives
When deciding what type of water reuse system is needed in a facility, a plant must define its objectives both from sustainability and cost perspectives.
- Select applications
Next, define the applications for which the water will be used. It is best to start with high-volume reuse applications that have lower water quality requirements, therefore requiring less treatment, such as landscape irrigation. By following this approach, the facility will achieve the greatest return on investment, as higher levels of treatment drive costs up.
- Determine Treatment Levels
Finally, determine the treatment levels required for the selected applications by measuring current wastewater quality to establish a baseline, and then compare that to the quality level required for the selected applications. This gap in water quality will determine the treatment intensity.
A food and beverage plant’s total water and wastewater costs can be significant. Employing the correct reuse technologies may result in significant cost savings for companies as well as a reduction in supply risk and benefits to the environment.